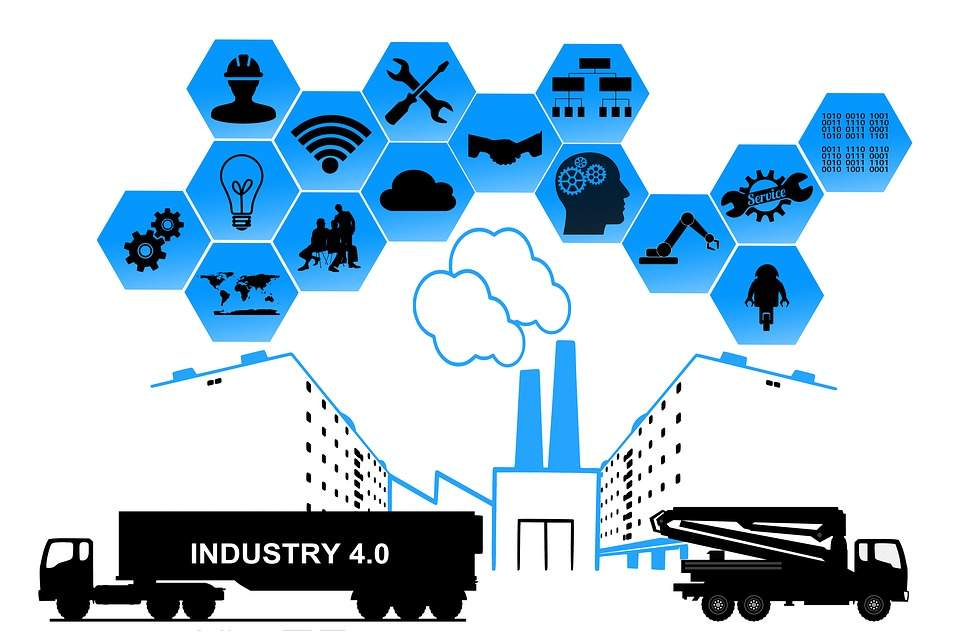
Mining businesses have always been subject to the commodity cycle, but fluctuations in supply and demand combined with increasing costs of production, the difficulty of accessing good quality seams and the declining quality of existing seams, mean that their margins have been under more pressure than ever over recent years.
Due to this, the industry has no choice but to find new, innovative ways of working, which will allow them to tackle these challenges head on and continue to operate sustainably and profitably.
According to a recent global research study by telecommunications company Inmarsat, technological shifts, such as using the Internet of Things (IoT) to turn mechanical processes into digital ones through automation technology, will be absolutely crucial to achieving this.
“The future of mining will ultimately rely on combining human creativity and experience with technology’s ever more sophisticated ability to collect, process and analyse vast quantities of data,” says Joe Carr, director of mining at Inmarsat Enterprise. “Those who do this most effectively will be able to overcome the industry’s current challenges through increased productivity and efficiency, and the redeployment of the human resources to more sophisticated roles as automated technology takes on more dangerous tasks.”
Elly Earls speaks with Joe Carr to find out what this future could look like and how the industry can get there.
Elly Earls (EE): In a nutshell, how can the IoT help mining companies navigate the challenges they’re facing?
Joe Carr (JC): IoT has a lot to offer the industry, but one of the areas it can make the biggest impact in is by turning mechanical processes into digital ones through automation technology. The industry remains very reliant on manual intervention, which is expensive, and automating processes will make an enormous difference to the bottom line, especially in developed markets like Australia and Canada.
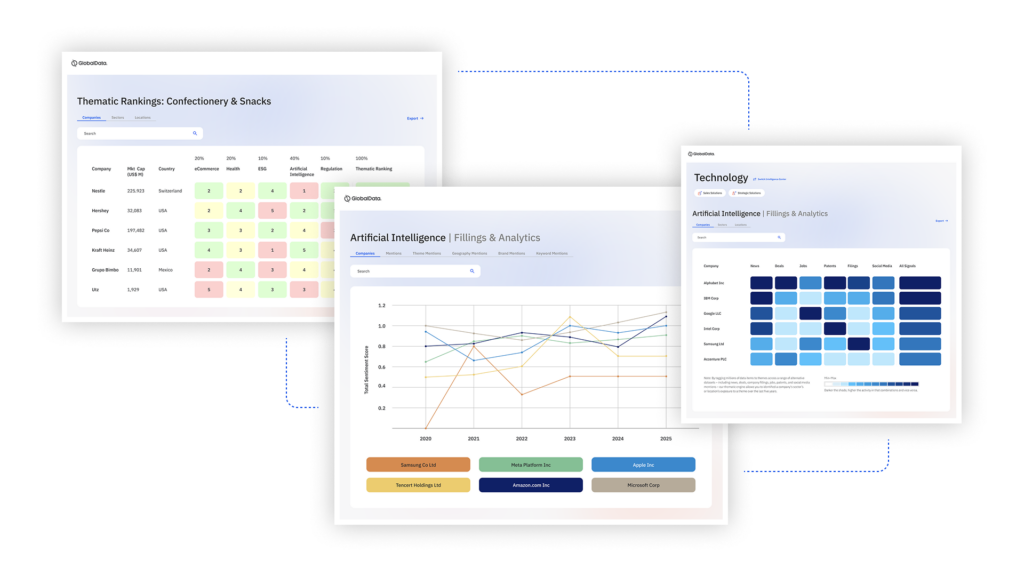
US Tariffs are shifting - will you react or anticipate?
Don’t let policy changes catch you off guard. Stay proactive with real-time data and expert analysis.
By GlobalDataReducing a reliance on manual labour and increasing automation will mean that mines will be able to operate around the clock, in a way that they’ve never been able to, driving new efficiencies and increasing productivity.
EE: Why is the mining sector so behind other industries when it comes to adopting new technologies?
JC: The industry can be quite risk averse when it comes to new technologies and there tends to be a bit of a ‘fastest follower’ approach with innovation, with many operators preferring to hold off until these technologies have proven themselves. But we’re seeing considerable interest building in IoT and other next generation technologies in the market and that’s backed up by our own research.
Although IoT deployment in the sector remains relatively low today, that won’t remain the case for long, and 55% of mining businesses expect to be leveraging the technology within the next 18 months. There is a clear recognition within the industry that IoT is crucial to mining’s long-term sustainability and competitiveness, so it’s only a matter of time until we see widespread adoption.
EE: What are the key innovations/technologies that have the potential to turn the mining industry around?
JC: With machines becoming progressively more capable of acting with little manual intervention, a future where adaptable and autonomous machines carry out the on-site, operational tasks of mining while human employees work remotely looks probable and profitable.
However, these technologies cannot function properly without robust connectivity. The remote location of many mining facilities means that terrestrial networks may be unreliable – assuming they’re available at all – and can be brought down by bad weather or natural disasters. A satellite communications network can offer a crucial failover for the terrestrial network, offering reliable, constant connectivity so that IoT solutions that depend on the transmission of data to a control room can continue to function.
EE: Can you give a couple of examples?
JC: Transport and haulage of mining materials is one application where IoT can achieve significant efficiencies. Sensors are currently used to collect data on how long trucks are kept waiting at different points within a mine, such as the time to be loaded. This data can then be analysed and used to improve the efficiency of haulage operations, for example reducing or increasing the number of trucks required hour to hour to ensure production is optimised around fuel usage, minimal maintenance time and haul distance.
Truck drivers in Australia can command salaries of $200,000+, and you need two and a half drivers per truck to keep operations running. If you’ve got 100 trucks per mine and you’re able to fully automate them, that’s a significant saving – not only from switching from a salaried employee to a capital expenditure, but also from the gained productivity of not having time when trucks are inactive due to breaks or shift changes.
EE: How crucial is it that mining companies increase their focus on data?
JC: Mining organisations need to look at data as the new gold, a high value asset which holds huge potential for mining organisations to reduce their costs, and establish the infrastructure and expertise to extract, share and analyse it. The growth in computing power means that more intelligence can be gained from data than ever before; and an increasing amount of this analysis will take place automatically within the devices and machines that are at the coalface, with people supervising and reacting to deal with issues the machines flag as important or critical. This is a key area in the innovation chain where mining needs to increase its focus. Machine learning and improved statistical techniques mean patterns and observations about data previously unseen can be revealed.
EE: Why is the industry struggling to both establish the infrastructure to do this and find people with the relevant skills?
JC: Like nearly every industry in every part of the world, there is a pressing skills shortage – many people just can’t learn fast enough to keep pace with the potential that new technology is bringing. However, mining faces some additional challenges. Its workforce is ageing. Older workers may be more experienced and have deep industry knowledge, but they are also less comfortable with digital tools and collaborative work.
Overwhelmingly, the mining industry has a skills shortage when it comes to developing and deploying IoT successfully. In our research, 64% of mining organisations reported that they lacked the necessary skills in cyber security, and a further 41% revealed that they did not have sufficient staff to analyse data effectively. Without these skills in place, mining organisations will continue to struggle to implement the infrastructure required to develop IoT solutions.
EE: How can these challenges be addressed? What needs to be done?
JC: We believe that partners will play a crucial role in the implementation of IoT solutions. With a clear lack of skills within mining organisations, 80% of businesses that we surveyed reported that they would use third-parties to help with the development and deployment of IoT technology. Mining businesses working together with organisations like Inmarsat and our partners, can leverage specialist expertise to bridge the skills gap and build successful, innovative IoT solutions.