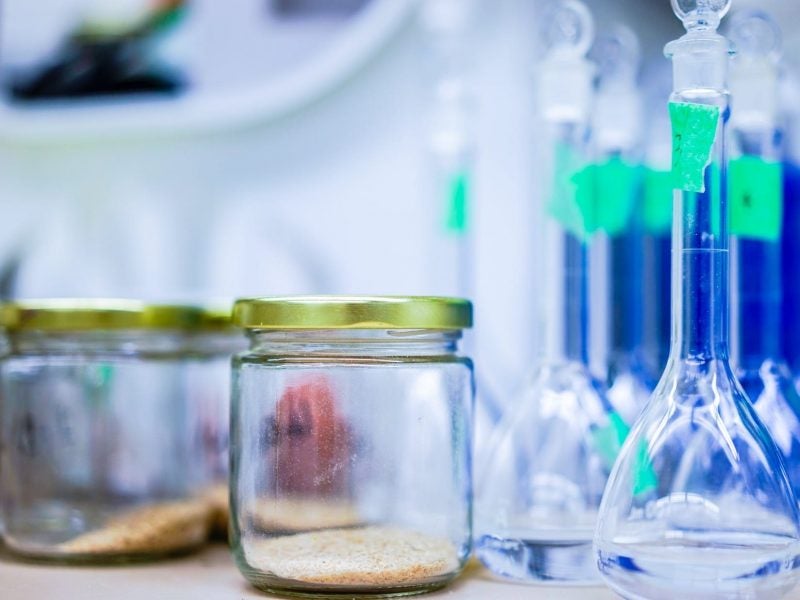
While the mining industry has not historically been known for its radical innovations and digitalisation, chemistry has long been used by operators for extraction and separation tasks, with new innovations serving to improve and expand the scope of this process.
Digital solvent extraction
With mining operations turning to digital platforms and applications to support operational improvements, Belgium-based chemical company Solvay has created what the industry has lacked – a digital platform dedicated to optimisation of copper solvent extraction.
Solvent extraction is used to concentrate and purify metals from mined ores; the company has tapped into the potential of digitalising this process with a platform called SolvExtract.
As the technique involves leaching soluble metals from the ore and separating them via solvent extraction chemistry, the process also stands out as significantly changeable, with varying quantities of metal extracted.
For this reason, Solvay has been using Minchem, a simulation model that predicts operational performance based on the analysis of samples collected from a particular mine. Then, based on the specific mining operation, the company creates an individual Minchem model, through which the web-based SolvExtract platform runs a simulation that comes up with improvement opportunities for the plant in case of low yield. The platform works with 20 to 30 collection points, from which it sends data to Solvay each hour.
This system allows operators to choose preferred adjustments based on the recommendations, with the process able to constantly track extraction performance and provide recommendations as often as once a day.
Solvay has said the software is part of an idea to create partnerships with mining sites to keep improving the platform by using essential data and feedback from companies.
Asteroid solvent extraction
Another pioneering area for solvent extraction is asteroid mining, a process dedicated to accessing bodies that contain nickel, cobalt, and platinum from inside asteroids and bringing those assets closer to mining operators.
As scientists from the University of Adelaide, Australia, are adjusting a solvent extraction technique that could help make asteroid mining economically viable, this long-researched asteroid ambition is closer than ever to becoming reality.
The asteroid solvent technique involves continuous-flow chemistry, where combinations of solvents are mixed with asteroid material to obtain the metals contained inside.
The process is intended to save large quantities of water, with development of a technology promising to use less than 10 tonnes of water to extract one tonne of metal as opposed to the usual use of hundreds of tonnes of water for similar processes.
According to the Adelaide researchers, the method can also take place in zero gravity and vacuum conditions, with capabilities currently being tested in-orbit as part of a partnership with the microgravity research and manufacturing company Space Tango.
With regards to finance, while launching costs of the technology will decline in the mid-term, they are likely to be relatively high to start with.
With the opportunity to mine asteroids from the solar system, potentially containing trillions of dollars of resources within, the prospect of such ventures is now gaining traction among governments and private companies.
Current asteroid mining expeditions include 17 missions for space resource exploitation, with the NASA OSIRIS-Rex mission to the Bennu asteroid expected to return with samples in 2023.
Rare earth element separation technology
With rising demand for rare earth elements, which are essential components in many consumer and industrial electronics, there is a need to optimise the separation of these elements.
Responding to market demand, in February 2020 rare metal miner Ucore announced the start of a mixed rare-earth element testing programme in partnership with Canadian operator Innovation Metals, aimed at processing element concentrates into separated oxides via Innovation Metals’ proprietary separation technology RapidSX.
Already developed and piloted, RapidSX is an accelerated solvent-extraction-based rare earth element technology for heavy and light elements with good potential for producing commercial-grade rare-earth oxides. The method is promising reduced processing time and plant footprint, reduced number of separation stages per circuit, start-up capital cost savings, and reduced time to achieve equilibrium – from weeks (in cases with conventional SX) to hours or days with RapidSX.
Innovation Metals’ planned test will involve mixed rare earth element concentrates produced from Ucore’s Bokan Project in Alaska, US, and other element concentrate feedstock.
This study will assess yield potential for rare earth element compounds and will look to obtain preliminary technical and economic estimates of the separation and purification process, including capital and operating costs.
If these tests of RapidSX are successful, Innovation Metals expects to conduct a more robust technical and economic evaluation during 2020/21 to assess the future impact of this technology on the rare earth metals industry.