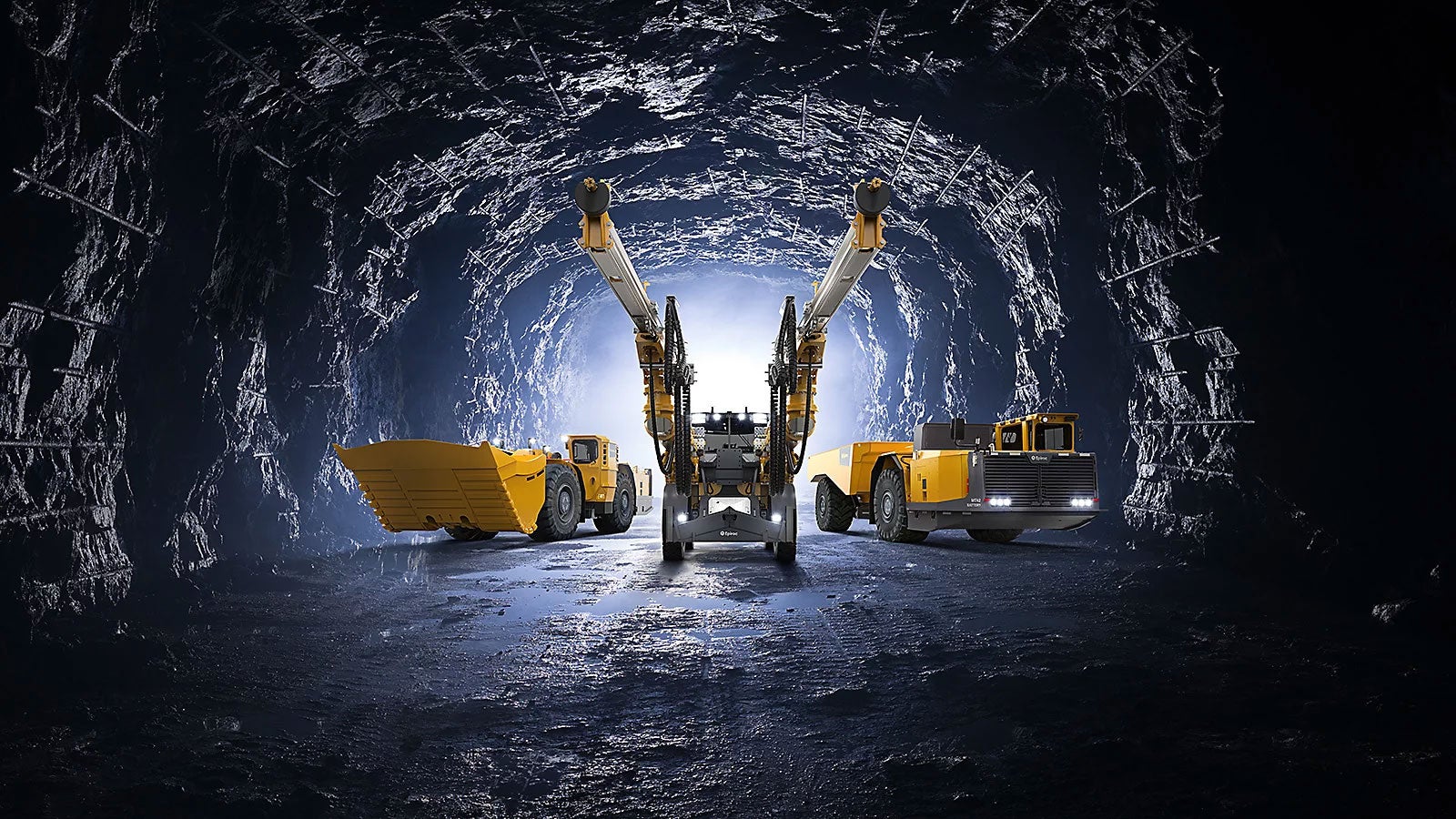
Battery electric vehicles (BEV) are electric vehicles that use exclusively chemical energy stored in rechargeable battery packs, with no secondary source of propulsion.
As miners attempt to cut their overall C02 emissions and mitigate the risks of diesel-powered vehicles on the health and wellbeing of their employees, the market for BEVs within the mining sector has proliferated.
BEVs are now considered proven technology, which has led takeup within mining operations to accelerate, with suppliers fast-tracking the production and expansion of their vehicle options. This is particularly the case for underground mines, where tethered or battery-powered load, haul, dump vehicles are becoming more common. Companies such as Epiroc, MacLean Engineering, Normet, and Sandvik now offer a range of different BEVs designed explicitly for underground operations.
Carbon intensity
Today, mining vehicles account for 30%-50 % (and up to 80% in some vital mining jurisdictions) of the total direct greenhouse gas emissions at a mine site. Globally, there are around 28,000 large mine hauling trucks in service, almost all diesel-powered, which consume roughly 900,000 litres of diesel and emit over 68 million tonnes of CO2 a year.
As miners continue to exploit global reserves, accessible deposits have become deeper and more expensive, with the development time to get to the ore significantly longer. To achieve net-zero mining, electrification of the fleet must occur. Removing 6.1 billion litres of diesel a year at copper mines (equivalent to 0.1% of global oil demand) would save around a quarter of their greenhouse gas emissions.
Both hydrogen fuel cells and BEVs offer two possible long-term solutions. However, with hydrogen technology still to get off the ground, BEVs offer the best solution.
Effectiveness of BEVs
The use of BEVs could not only save high costs on ventilation and cooling but also improve worker health and generate a fraction of noise of traditional diesel-powered machines. On average, the switch to a fully electric mobile fleet results in a 40% to 50% reduction in ventilation demands. This is equivalent to considerable cost savings in both power used and ventilation infrastructure.
Other benefits include maintenance costs, with battery vehicles having 25% or fewer parts less than diesel propulsion systems.
An example of BEVs’ successful deployment is the Newmont Goldcorp’s Borden Lake mine in northern Ontario, which now boasts 16 battery-electric utility vehicles from MacLean Engineering, including bolters, a block-holer, cassette carriers, and scissor lifts. Here, both BEVs suppliers and the miners have worked closely together to adapt the mine to the needs of BEVs.
Collaboration
One of the best ways for BEVs to gain greater prominence within mining circles is through collaboration between miners and vendors, facilitating an increase in both market share and the infrastructural changes required within the mines to allow for the use of BEVs.
The International Council on Mining and Metals’ (ICMM) Innovation for Cleaner, Safer Vehicles (ICSV) initiative exemplifies this collaborative approach. ICMM members represent approximately 30% of the global metals market, with over 650 assets in more than 50 countries, offering a critical mass for change that creates market pull.
This, they argue, will build the widespread confidence needed to accelerate the level of innovation investment required to scale up commercial solutions for the industry and meet the initiative’s ambitions.
Sarah Bell, director of health, safety, and product stewardship at the ICMM said: “Our membership makes up around 30% of the total metals market and makes up approximately 46% of copper; 27% of gold; and 42% of iron ore produced globally. The signals that can be sent through this program are strong.”
The initiative is working towards the achievement of three main ambitions:
- Introduce greenhouse gas emission-free surface mining vehicles by 2040.
- Minimise the operational impact of diesel exhaust by 2025.
- Make vehicle collision avoidance technology available to mining companies by 2025.
The ICSV recognises that mining companies can’t achieve these outcomes alone, but by working with industry partners, they have an opportunity to succeed.
Vendors
To facilitate this change, a range of reputable vendors are needed to supply the transition to BEVs. Several companies have come to the fore, offering a range of options for miners in their underground operations.
Sandvik Load and Haul is a prime example. It now offers three battery-electric trucks and loaders – a 50 tonne truck (the Z50), a 10 tonne loader (the A10), and a 4 tonne loader (the A4) – and battery-electric drill rigs. Sandvik received orders for BEVs amounting to about SEK140m in June, marking Sandvik’s highest ever order intake for mining BEVs in a single month, demonstrating an increased take-up amongst miners.
Epiroc has been on a similar trajectory. In 2019, the company launched a 4 tonne loader for the Chinese market, the Scooptram ST4 Battery. This model will also be more widely available soon and the company has announced plans to expand its already large BEV fleet with new equipment launches.
For BEVs, an essential factor is the standardised charging of the batteries; mines need to have universal charging stations for all deployed vehicles. Both Sandvik and Epiroc have decided to use a standard from the automotive industry to ensure that its vehicles can be charged on multiple units.
Future prospects
However, it is essential to note that BEVs alone will not act as a silver bullet. They are not a one-size fit all solution to all mines, with some mines unsuitable for BEVs and some unable to afford the new fleet of BEVs. Additionally, early adopters of EVs in mining ( typically with trolley EVs) had to scrap their trolley EVs because manufacturers would no longer maintain them.
Despite electrification allowing for safer operations, automation, and regenerative braking to boost efficiency, these efficiencies will not offset the increased energy intensity of deeper, more remote, and lower-grade mines. This makes collaboration even more critical to support mines unable to fund an electric fleet independently.
There is significant promise in the progress companies such as Epiroc and Sandvik have made in providing high-quality BEVs that considerably improve mining performance, and with collaborative initiatives such as the ICSV initiative, a greater uptake and deployment of these vehicles could allow more and more miners to adopt the technology within their mines.