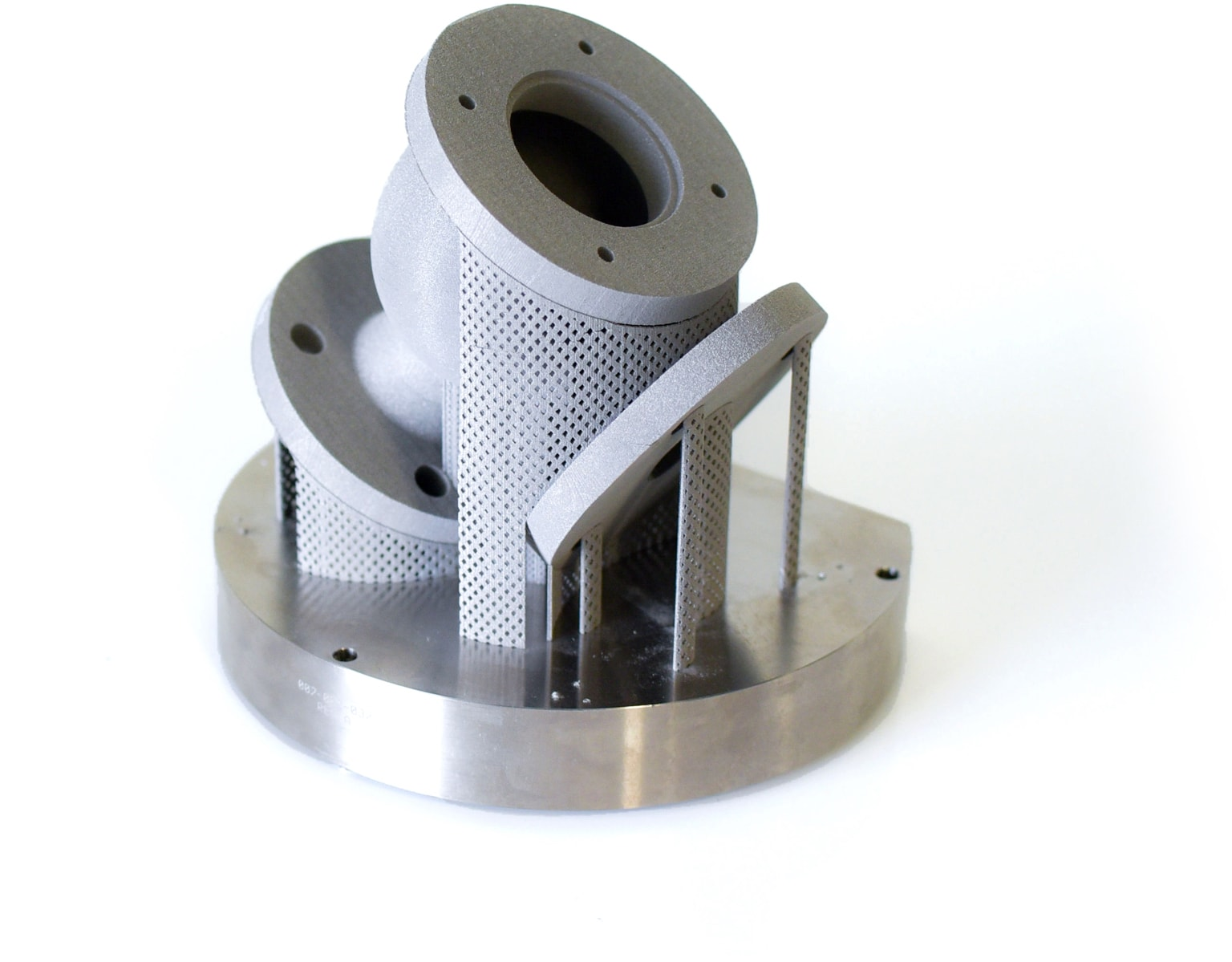
As 3D printing becomes increasingly advanced, more and more industries are looking into its huge possibilities. Mining is no different, as 3D printing offers an economic and efficient way to manufacture essential components.
Fortescue Metals Group (FMG), an Australian iron ore mining company is keen to take advantage of these benefits. Last October, they announced that they had teamed up with 3D printing company Aurora Labs as part of a 12-month agreement to develop 3D printing in the mining industry.
Dave Budge, CEO of Aurora Labs, explains how the technology is developing and what it could mean for the mining industry.
Molly Lempriere: Could you tell me a little about 3D printing and its benefits?
Dave Budge: For us in the mining sector, it’s about replacement parts and there are two components to that. With our technology we’re looking to have a machine in the marketplace in the future that could potentially create up to a tonne a day worth of parts. If you can print a part, instead of having to wait anywhere from a couple of weeks up to potentially 12 to 18 months for a part to be delivered, then that would change enormously your inventory requirements.
Some mining companies have enormous inventories, upwards of $4bn, so if they can print a part in a day and they don’t need 12 months’ worth of stock it could make a huge difference. All of a sudden they can print parts on demand, or alternatively they can have a minimal stock on hand and then just print replacement parts.
There are two significant ways that this technology impacts the mining sector; firstly, there is the possibility of having significant reductions in cost. A lot of the modelling that we’ve done shows that you can have up to a 50%, and in some cases a 90%, reduction of cost of parts by printing using our processes. With traditional manufacturing you’d find it difficult to get that significant step change in cost in virtually any circumstances.
Furthermore, it allows for a rapid redesign of components. So for example, if you have a pump that wears out very, very rapidly, and instead of asking an original equipment manufacturer to modify that pump, what a company could do is modify their own pump. It could design a modified component for the pump so it doesn’t wear out so rapidly
ML: Could you tell me a little about your Rapid Manufacturing Printer and how it’s different from others?
DB: Our process is different in that instead of printing a single layer at a time, it prints multiple layers at the same time. Basically, the printer allows a series of separate layers to be printed simultaneously, and the advantage of this is that it allows a very, very high production rate while maintaining a very, very high quality. That’s I guess the primary difference between our technology and existing ones, it allows us to potentially build something in a fraction of the time.
Currently, the world’s fastest SLM [Selective Laser Melting] machine as we understand prints about ten kilos a day. Our machine will be approximately two orders of magnitude greater, so about a hundred times faster than what was, until recently, the world’s fastest machine.
The reason this is important is when we look at the cost of manufacturing the part, generally with traditional 3D printing the machines are very expensive and they’re very slow. Of course if you have a very expensive, very slow machine then the part that you’ve manufactured is very expensive. With our machine because it’s so fast, it will allow parts to be produced potentially cost competitively with traditional manufacturing which is really a significant step.
ML: What sort of scale are the products that you can 3D print?
DB: Our current machine that we have in production now, which is our first Rapid Manufacturing Printer, will build about half a cubic metre, so it’s about 450x450x450mm. The next machine that we’re looking to build, which is the larger RMP2, will be able to build about 2.5×1.5m, so that’s quite a large build area.
Most of the clients we’ve spoken with said that about 90% of their parts would fit into that envelope, so it’s quite a significant size as well.
There is another group we’ve been speaking to for a while as well, who say that they’re interested in buying a machine that can print parts up to 30m long, they’ve been discussing that as an option for a while. So the benefit with our technology is its ability to scale. So if a customer came to us and said we would like to have a machine that could be extended, we could build a machine that could do that.
Are there any safety concerns around using 3D printed components?
DB: That dives into another sector of our business we’ve been developing, which is what we call Digital Part Certification. It’s essentially a process whereby the part can be printed and certified in real-time, while it’s being printed.
I guess the short answer to that is no, but honestly products that are going to be printed will also need to be certified, whether they’re using an internal process like the one we’ve developed, or externally certified by a group like DNVGL.
Certification in 3D printing is really critical because without certification what you have is a paperweight basically; it’s critical for it to have certification for it to be a functional, usable part.
ML: Are there any environmental impacts to choosing 3D printing over traditional production?
DB: Actually there are quite a few that most people probably aren’t aware of; I’m keen to mention them because they’re all positive.
The first one is that 3D printing is very energy efficient, it uses far less energy than traditional manufacturing processes. To take powder and convert it into a part takes a lot less energy.
The other side of it is if you make the components lightweight, which is possible utilising 3D printing technologies, there are other benefits. Some of the things in the aerospace industry, for example, they have shown that if you can make a part of a plane lose a kilo in weight then it saves an enormous amount of fuel over the course of its life. The same thing applies to car parts and other forms of transport, so making lightweight components is also economically and environmentally a very good thing indeed.