Exploration and extraction technology refers to all technologies employed during the life cycle of a mine. They include GPS, new drilling technologies, 3d mapping and geomodelling through to remote operation centers, autonomous equipment and process controls. These technologies can improve the success of exploration activities, reduce the environmental impact of mining and improve productivity of operational mines. Innovations have accelerated recently due to the need to enhance safety, improve productivity and control costs, with 3,000 patents filed and granted in the mining industry in the last three years alone, according to GlobalData’s report on Innovation in mining: ore pre-treatment. Buy the report here.
However, not all innovations are equal and nor do they follow a constant upward trend. Instead, their evolution takes the form of an S-shaped curve that reflects their typical lifecycle from early emergence to accelerating adoption, before finally stabilizing and reaching maturity.
Identifying where a particular innovation is on this journey, especially those that are in the emerging and accelerating stages, is essential for understanding their current level of adoption and the likely future trajectory and impact they will have.
45+ innovations will shape the mining industry
According to GlobalData’s Technology Foresights, which plots the S-curve for the mining industry using innovation intensity models built on over 81,000 patents, there are 45+ innovation areas that will shape the future of the industry.
Within the emerging innovation stage, tunnel ventilation systems, remote tunnel monitoring, and mine drainage systems are disruptive technologies that are in the early stages of application and should be tracked closely. Lithium recovery, battery metal recycling and tunneling, and anchoring machine are some of the accelerating innovation areas, where adoption has been steadily increasing. Among maturing innovation areas are hydrometallurgical extraction and hybrid industrial vehicles, which are now well established in the industry.
Innovation S-curve for the mining industry
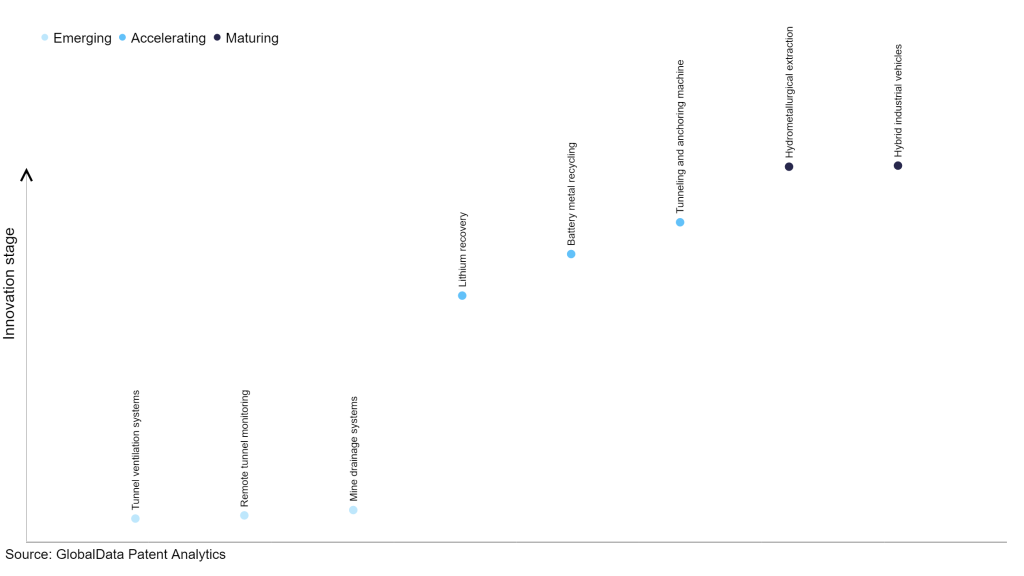
Ore pre-treatment is a key innovation area in mining
Ore pre-treatment, which is usually performed before grinding, creates intergranular cracks that make grinding easier, resulting in a reduction in grinding energy. Some of the pre-treatment methods include thermal, chemical additives, electric, magnetic, ultrasonic, bio-milling and radio frequency. As quality resources dwindle and more fine particles need to be processed in a stable and optimized manner, pre-treatment becomes necessary. Demand for energy-efficient grinding pre-treatment methods will increase as high-grade resources deplete and environmental constraints related to reject disposal become more stringent.
GlobalData’s analysis also uncovers the companies at the forefront of each innovation area and assesses the potential reach and impact of their patenting activity across different applications and geographies. According to GlobalData, there are 40+ companies, spanning technology vendors, established mining companies, and up-and-coming start-ups engaged in the development and application of ore pre-treatment.
Key players in ore pre-treatment – a disruptive innovation in the mining industry
‘Application diversity’ measures the number of applications identified for each patent. It broadly splits companies into either ‘niche’ or ‘diversified’ innovators.
‘Geographic reach’ refers to the number of countries each patent is registered in. It reflects the breadth of geographic application intended, ranging from ‘global’ to ‘local’.
Patent volumes related to ore pre-treatment
Source: GlobalData Patent Analytics
JFE, Metso, Kobe Steel, POSCO, and Vale are among the leading patent filers in ore pre-treatment.
Metso has a Feed Pre-treatment System (FPS) that expands the range of sulphide concentrates and residue materials that can be treated in a roasting plant. The FPS can help roasting plant operators meet critical operational key performance indicators such as increased capacity and product quality. Furthermore, there are environmental benefits such as lower dust emissions and fewer tailings produced. Sulphur and zinc-containing residues, such as sulphur residue from the Metso Outotec direct leaching process, sulphur residue from the Metso Outotec Pure Jarosite process, can be recycled using this process. Similarly, the company's BIOX process for treating refractory gold concentrates has produced over 22 million ounces of gold. In various climate conditions, BIOX plants have treatment capacities ranging from 20 to 2,137 tonnes per day of flotation concentrate.
In terms of application diversity, Zijin Mining Group leads the pack, while Vale and Metso stood in the second and third positions, respectively. By means of geographic reach, Zijin Mining Group held the top position, followed by Teck Resources and Kobe Steel.
To further understand the key themes and technologies disrupting the mining industry, access GlobalData’s latest thematic research report on Mining.
Data Insights
From
The gold standard of business intelligence.
Blending expert knowledge with cutting-edge technology, GlobalData’s unrivalled proprietary data will enable you to decode what’s happening in your market. You can make better informed decisions and gain a future-proof advantage over your competitors.