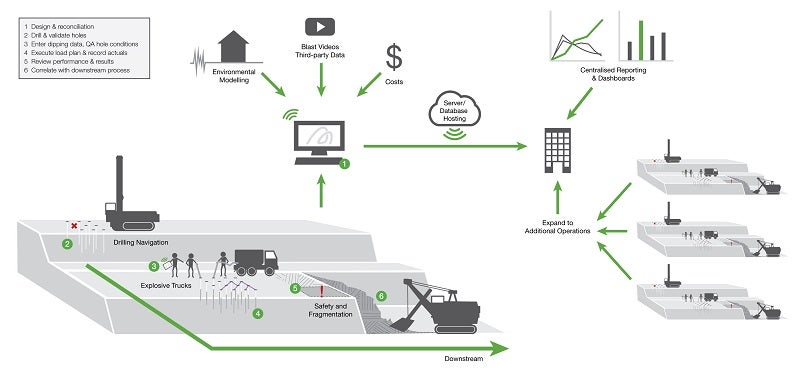
Practices around drill and blast operations vary greatly from site to site, particularly when it comes to recording actuals data.
At many sites, actuals data such as hole depth, presence and amount of water, hole temperature and loading are recorded on paper. At other sites, some of this data may not even be collected.
Tracking your actuals provides a number of benefits. Recording this information helps with everything from design conformance and blast outcome investigations to maintaining regulatory compliance.
However, while simply collecting and recording your actuals is crucial, making them digital will enable you to increase efficiency across your entire drill and blast operations.
3 key reasons to have a digital record of drill & blast actuals
Data accessibility
Actuals data is valuable. But if you collect it on paper, it is likely to sit in a filing cabinet or on someone’s desk.
For situations where you need to understand the ‘why’ behind a decision or scenario – why digging is hard at the toe or investigating a fume event – researching a particular blast can take several days (and usually more) with paper drill and blast records.
The digital capture and storage of drill and blast data enables quick access and analysis of blast data as it is stored in a central location. This significantly cuts down investigation time.
Accessibility for future learnings
Beyond blast investigations, increased data accessibility enables you to apply your learnings to future blasts.
Many mines around the world are not commonly using drill and blast data from previous blasts to inform future plans and designs. This is primarily due to the practicality of accessing and using paper records within the demanding time constraints of the mine operations.
But not taking advantage of this data is leaving a lot of efficiency (and money) on the bench.
When these records are available and accessible through digital means, engineers and blast crews are able to more readily use this data in their day-to-day processes. For example, you can easily compare a current blast design to the inputs and outputs of a blast on the bench above – allowing you to take similar conditions, such as rock type or water, into account.
Correlation of data
Access to digital blast data also allows you to better correlate blasting inputs and blasting outputs.
Unfortunately, for most mine sites, drill and blast data – such as drilling data, loading data, vibration readings, drone footage, and even ‘digability’ and shovel strain data – is heavily siloed as a result of how it is stored.
In contrast, digital data stored in a central location becomes a ‘one-stop-shop’ for a given blast’s data. This allows for proper analysis and record keeping. And even better, with the proper tools, the data can be spatially correlated and viewed in 3D, allowing for a deeper level of understanding.
When blasting inputs are captured digitally and compared to blasting outputs, engineers and crews are able to correlate certain blast KPIs, such as fragmentation or vibration, back to the blast inputs. This injects your blasting program with empirical evidence to improve operations rather than relying solely on anecdotal evidence.
Productivity gains
A vital piece of the drill and blast process is follow-on reporting – for both the greater mine operation and also regulatory requirements. However, across the globe, we hear about how this is a time sink for site personnel.
With digital records of actuals data, there is an opportunity to streamline reporting, which will reduce the amount of time blast personnel spend on tedious paperwork-related tasks.
Digitally recording explosive usage, drill actuals, load actuals and shot firing times can ensure that when data is input and recorded, it is only done once. When a piece of blasting data is input in a digital system, it can be set up to propagate to all the appropriate reports. This eliminates duplicate entry of blast data. Additionally, certain data can be pulled directly from equipment, which by-passes manual entry entirely for that data.
Imagine the added advantage to a blast crew of significantly reduced paperwork. It enables more time to be spent optimising for a particular outcome, potentially being able to load and shoot larger patterns, and importantly, improving safety by relieving stresses on blasting crews.
The digital advantage
With digitally captured drill and blast data, your blast crew can increase efficiency across the entire blasting operation. And, if you want to make the most out of your digital blast data, you need to access this data in real-time.
A comprehensive blast management system such as Maptek BlastLogic makes life easier for staff and improves the bottom line for the mine.