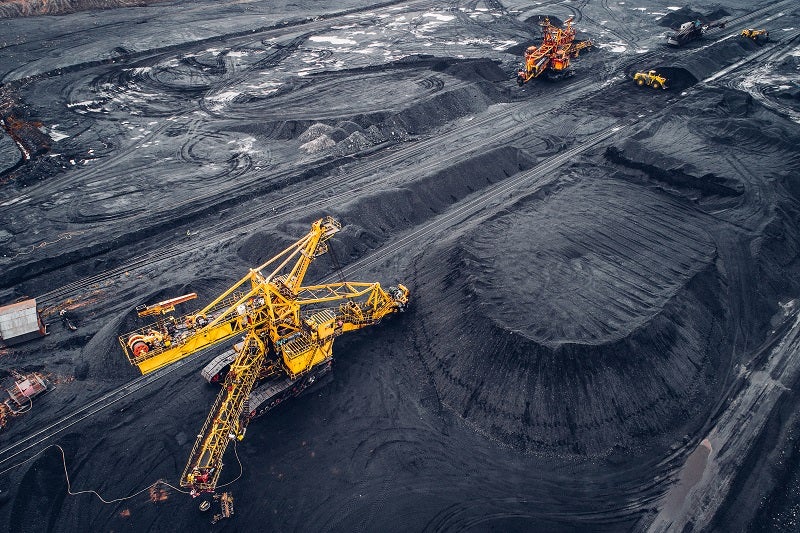
When it comes to measuring products, whether it’s liquid or solid, accuracy is essential. For years, mine operators have turned to ultrasonic devices to gain this information, utilising ultrasonic waves to detect the quantities within a bin, hole or stockpile.
But this approach has come with a range of challenges for operators, namely the interference that the external factors can have on an ultrasonic devices reading. Ultrasonic level measurement, which use a pulse signal targeted towards an object which is then reflected and echoed in return to the sender, is susceptible to the environment. In other words, it can be disturbed by dust, heat, and other atmospheric elements.
Fortunately, there is an alternative. Like ultrasonic equipment, radar level measurement devices are non-contact instruments used to measure liquids and solids throughout the mining process. They send out a microwave beam that hits the surface, reflects and allows the equipment to work out the quantity.
“Radar level measurement devices work on the same principal as ultrasonic, which is not in contact with the material, but they use different methods,” explains John Leadbetter, managing director at leading mining equipment provider Vega. “They are fast-reacting, travelling at the speed of light and, crucially, unlike ultrasonic equipment, these devices are immune to dust, heat, wind, snow, and other environmental effects.”
Other advantages of radar level measurement devices over ultrasonic equipment are the speed of response, accuracy and reliability, an essential trait for a device which is used throughout the mining process.
“Operators will use these from the pit, where they mine the ore from, to the port, where they load the ore onto the ships for export to other countries,” says Leadbetter. “As well as measuring pressure and airflow, this equipment provides a way of monitoring how much dirt is moving through the plant to check how much of it can be turned into product and sold to customers.”
The latest innovations
With each year, the technology applied to radar measurement improves. For Vega, this means providing operators with the latest innovations through their VEGAPULS 64 and VEGAPULS 69 devices.
The VEGAPULS 64, a sensor for the continuous level measurement of liquids, offers a range of special advantages when used with small tanks or narrow spaces, as well as an improved signal focus to enable use in vessels with many installations.
The VEGAPULS 69, meanwhile, is a sensor for the continuous measurement of bulk solids under different process conditions. Ideally suited for level measurement in very high silos, large bunkers and segmented vessels, it provides good signal focusing, a simple setup process, and reliable measurements.
“We sell in excess of 100,000 units of these models a year, worldwide,” says Leadbetter. “They are one of our most popular products and we have spent the last five or six years ensuring we develop it correctly and to the customer’s satisfaction.
“Vega has had these particular models in the marketplace for five years but we’ve been making radars since 1991. Because of these years of experience, we’ve been listed as a preferred supplier in a lot of Australian mining operations.”
With Vega’s radar measurement, operators are getting a unit that is not only reliable and accurate, but very well supported. According to Leadbetter: “We carry stock of these units in Australia and have a lot of experience with them. We have also manufactured the equipment so that you don’t need external technicians to set it up.
“While these units have been on the market for a few years and have proven themselves, we have continuously improved them to meet our customer’s requirements and ensure the best possible results, every time.”