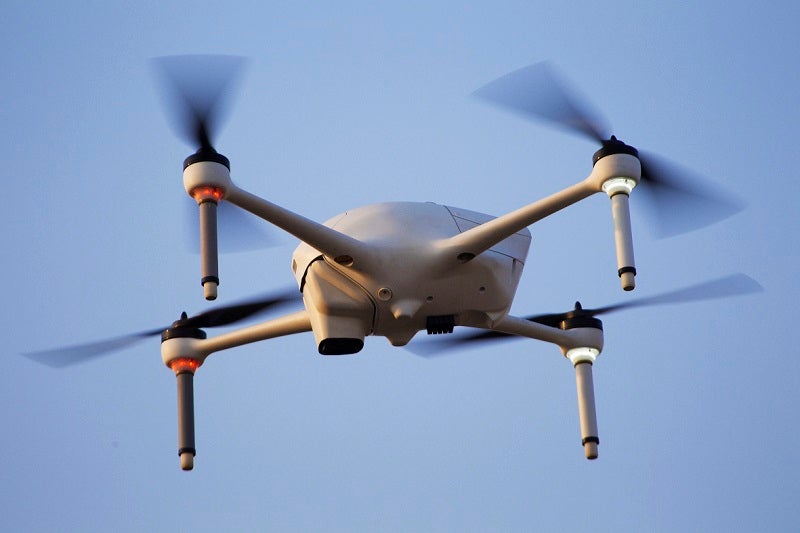
The popularity of unmanned aerial vehicles (UAVs) across the mining industry has grown substantially in recent years, with over 60% of mines in Europe and Australia investing in drone technology. The technology has applications across the sector including safety operations, as drones are able to reach areas humans cannot.
Founded in 2014, Airobotics boasts a pilotless drone solution, the first of its kind in the global market. Dan Ward, director of technical engagement at Airobotics, tells us about developing digitalisation and automation strategies using drones.
Umar Ali (UA): Could you tell me a little about your drones and what makes them special?
Dan Ward (DW): Our automated drone system comprises of Optimus, an industrial-sized multi-tool drone, a completely automated base station from which the Optimus drone launches and lands on its own without any physical human intervention and the Airobotics Software, which enables users to visualise, process and analyse aerial data.
Airobotics’ robotic airbase, multi-sensor drone, and AI-driven analytics automate the digitisation of sites and cities through high-frequency data collection, processing, visualisation and analysis to reveal critical business insights.
The drone system has the unique capability of swapping its own batteries and payloads using a robotic arm, allowing for a diversity of payloads and mission types. No other drone company can purport to do this without human intervention.
UA: How does Airobotics’ automated platform help with mining safety?
DW: The Airobotics automated drone system eliminates the need for drone pilots to be available and manage flights on site. As a result, the major safety benefit is the ability for continuous inspection, survey and mapping, and compliance management in industrial settings, without exposing personnel to potential hazards in the work environment.
We recently made Australian aviation history by obtaining the nation’s first and only Civil Aviation Safety Authority (CASA) approval to operate automated multi-rotor drones from its Remote Operations Centre beyond visual line of sight (BVLOS) with no aircrew needed at the client site.
Standard VLOS operations requires a remote pilot on site, who often needs to enter dangerous areas to maintain a direct line of sight with the drone. By removing the need for VLOS operations, BVLOS drone flights greatly improve the safety of the site operations.
Automation not only facilitates safety, but it also replaces mundane tasks.
When personnel are freed up from mundane tasks that can be completed through automation, not only can they perform more valuable roles such as data analysis, but they will have new opportunities to re-channel their expertise into other tasks and strategies that have a greater impact on the operation.
UA: How can you see drone technology progressing?
DW: Initially, drone technology was largely developed for recreational use, and whilst it has matured over the last few years, there are still some ways to go in terms of development for industrial usage and certainly, automation.
We believe drones will be widely used across many industries in the coming years and adopted in three phases. First, which we are already in, is deploying systems in safer, unpopulated environments, such as mines, refineries, sea ports and fabrication facilities.
Take the mining industry for example, we believe that mining operations are increasingly looking to deploy automated drones, the most compelling arguments driving them are not the tactical or economic ones, as persuasive as those are. Rather, automated drones are poised to become an essential strategic part of mining’s future, providing an integrated, holistic solution that bridges the gap between decision-makers and the critical data they rely on, quickly and accurately.
Secondly, after accumulating hundreds of thousands of flight-hours with increasing reliability and safety, would be to use these systems in urban environments. Applications would initially be around emergency response.
The third step of this vision is full commercial everyday use. Drone systems will be situated in various locations around the city serving multiple customers in applications like infrastructure and property inspection, real estate, construction, disaster recovery and more.
The greatest and most important hurdle we had to overcome is regulation. If drone operators and drone companies can prove their safety case and show regulators that they are not a risk for people and for businesses, regulators will progress and enable the wider adoption of this tool.
UA: How have mining companies responded to drone technology so?
DW: Mining companies have been utilising drones as part of their daily survey operations for several years now so drone technology is not inherently unfamiliar.
Drones are becoming an integral tool on site, replacing manual inspections in the most hazardous areas and collecting critical information, while drastically reducing the time and manpower required. With added automation capabilities, the operational advantages brought on by drones are further augmented with consistent and reliable data capture, download, processing and collaboration.
The concern with the use of drones on mine sites is not so much the lack of belief in the technology to deliver value but rather, the safety and regulatory aspects of operating drones on site.
It is not unusual for surveyors or other mining professionals to double-up as drone operators on site and unfortunately, drone incidents involving other mining equipment and/or personnel are not uncommon either.
This is a training and resource issue, which can be mitigated with an automated drone system managed offsite by regulatory-approved, professional drone pilots. This move is definitely welcomed by the industry that holds safety in the highest regard.
UA: Were there any challenges in developing drone solutions for mine safety?
DW: When Airobotics first started, we certainly faced some challenges in terms of how we could realise our drone capabilities. The first was the availability of specific drone components that could stand up to industrial standards – they were not where we needed them to be. As a result, we decided on the path of in-house product design and manufacturing, which led us to where we are today.
The other challenge was regulations. Being the leader in this space always placed Airobotics at the forefront with regulators when it comes to accepting and approving that drones can indeed fly safely from a remote operations centre. It took the team years and hundreds of thousands of hours of test flights and detailed supporting documentation to prove our systems’ capabilities.
As drones continue the trajectory from ‘recreational toy’ to ‘indispensable industrial tool’, we expect to see further enhancements in related technologies. For example, improving battery life to fly longer and cover larger areas and new, lighter payloads with higher-accuracy data-capture, and increased diversity in applications.