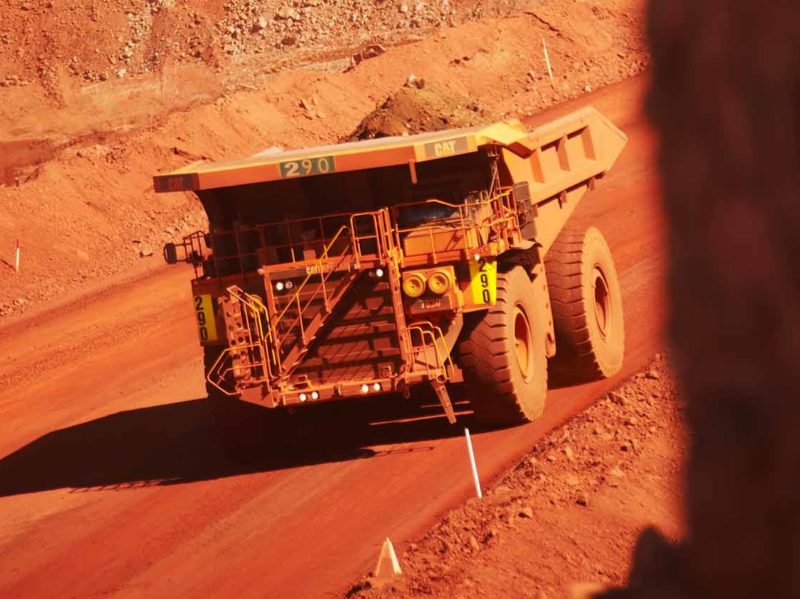
Technology is set to revolutionise the Australian mining sector. A new report commissioned by the Minerals Council of Australia (MCA) has found that over the next five years, more than 77% of jobs in the country’s mining sector will be altered by technological innovations, increasing productivity by up to 23%.
According to MCA’s CEO Tania Constable, Australia’s education and training system will require the greatest transformation. She anticipates the modernised structure to offer “enhanced movement between universities and the vocational education sectors”, combining traditional mining skills with ‘the latest scientific, technical and trade skills’ such as data analytics, computing and change management.
Future degrees are also expected to focus on collaboration, creativity, and social science skills in response to ‘changing community expectations’, offering student’s higher certifications and fit-for-purpose degrees.
Speaking with Sam Spearing, director of the WA School of Mines Kalgoorlie, he says that “life-long learning will be essential” in the new technological landscape. According to Spearing, the post-secondary school sector will likely see the greatest impact due to the “need for seamless educational pathways from school through the TAFE and into Universities”.
“The tertiary education system wants to keep ahead,” Spearing says “I don’t think there are downsides, but some of the workforce will need to be upskilled and supported by the employers whilst this is being done.”
Exploration: autonomy heralds adaptability
Current exploration design is hindered by the fact that it is based on retrospective and static methods, with only minimal adjustments possible during drilling. However, new technologies such as geo-spatial data, 3D mapping and hyperspectral core imaging allow the material drilled to be continuously monitored, while tools such as autonomous drills allow exploration methods to be adapted in response to information gathered. Companies already employing such technology include Rio Tinto and BHP, the former with its 3D mapping technology and the latter with its downhole assay.
Rio Tinto’s system comes under its Mine of the Future programme, and works to identify the size, location and quality of underground deposits in real-time, accessing data from automated trucks and drills on the site. BHP’s downhole assay, deployed at their Pilbara operations, works to distinguish between resources and waste material, and is anticipated to save the firm more than $10m on drilling and assay costs at sites in Western Australia.
Processing: drones and digital twins will streamline ops
A poorly run processing plant can prove a huge drawback in mining operations. Depleting high-grade ore deposits, breakdowns and poor scheduling are just some of the obstacles facing a streamlined system. EY found the integration of tools such as ore-sorting technologies, drones and digital twins could help to improve efficiency and product quality.
Ore-sorting technologies work to separate valuable materials from waste and reduce the amount of material that requires processing. Drones, advanced analytics, digital twins and an Integrated Operating Centre (IOC) provide a means to better manage feed presentation, optimise plant operations and shift maintenance strategies from reactive to predictive. EY estimated that this section of the industry could see a rise of 7%-15% in asset productivity improvement, a 10%-15% reduction in processing cost and 8%-20% overall productivity improvement.
Trading: end-to-end transparency key
With consumers’ rising awareness of the ethical pitfalls of mineral supply chains, there has been an increased demand for transparency in the sourcing and processing of materials. Blockchain technology provides an efficient means of tracing metals from extraction to processing, lending full visibility to the process.
Diamond company DeBeers has developed a blockchain platform called Tracr, used to track the progress of their diamonds and create a digital trail for each physical diamond. Such a platform helps to establish an ‘end-to-end baseline of trust’ that is entirely novel to the industry, demonstrating the capabilities of technology to overcome challenges of authenticity and compliance.
Speaking to the Tracr team, they say the technology “ensures immutable end-to-end traceability”, while allowing users to maintain full control of their own data.
“Blockchain allows the automatic detection of fraud, reducing instances of round-tripping and double-financing” the team says, adding that “the increased visibility and trust will facilitate access to financing and potentially improved interest rates, while a decreased reliance on email and paperwork will cut operating costs and improve efficiency.”
While the system is currently a B2B platform, the team also said they anticipate B2C applications to be developed in response to consumer needs.
Transport: autonomy means reduced stoppages
Current transport systems are susceptible to human-induced errors or delays, and one unreliable vehicle can have a domino effect on downstream operations and rack up costs.
Technology such as broken rail detection and digital twins allow for maintenance to become predictive rather than reactive, catching problems before they have significant effects further down the line – minimising interruptions and streamlining shipments.
Autonomous vehicles allow operators to work offsite and thus remove the need for operator-induced stoppages. Rio Tinto began using autonomous trains for their Pilbara operations in 2017 and have reported improvements in safety and a reduction of bottlenecks and cycle time. EY predicts that introducing such vehicles could lead to an improvement in asset operating time of up to 20%, and an overall productivity improvement of between 3%-15%.
End-to-end value chain: artificial intelligence for optimal planning
Optimisation of planning and scheduling can be achieved through IOC’s and digital twins, allowing various scenarios to be trialled and workers to select the optimal planning route to increase productivity.
Australia BHP uses Artificial Intelligence (AI) to schedule track movements and the dispatch of trains carrying iron ore between their mines and Port Hedland, something that has thus far helped BHP to manage stockpiles and ensure deliveries are correct and on time.
Mining operations: electric mines avoid underground dangers
Technology has already allowed for significant progress in the field of mining safety, which as Spearing says is “of paramount importance.” Current underground minesprove hazardous environments, given the threat of falling rocks, poor ventilation and exposure to heat and gas. In particular, the electrification of vehicles will mean workers’ will no longer be exposed to the carcinogenic Diesel Particulate Matter emitted from traditional vehicles.
Canadian firm Goldcorp is in the process of constructing a fully electric mine, complete with battery-operated drills, electric haul trucks and electric bottlers. The company has estimated the operation will eliminate around two million litres of diesel per year and reduce greenhouse gas emissions by 70%.