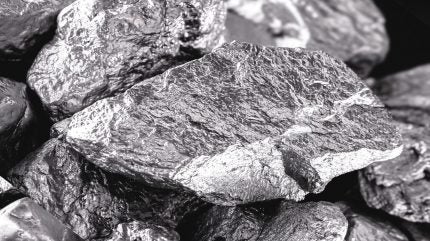
Xerion Advanced Battery has announced the launch of pilot-scale production at its facility in Dayton, Ohio, US, using its proprietary DirectPlate Molten Salt Electrolysis (MSE) cobalt refinement technology.
The DirectPlate MSE technology was initially developed for refining and synthesising battery components. It introduces a single-step, continuous process that significantly reduces the complexity and cost associated with cobalt refinement.
The pilot-scale production facility has a five-tonne capacity to refine its process ahead of planned expansions toward commercial-scale output.
The DirectPlate MSE approach enables the transformation of crude cobalt hydroxide directly into high-purity cobalt metal with high efficiency.
In lab-unit testing, Xerion achieved greater than 99% pure cobalt metal output with yields exceeding 98%, producing more than 100kg, an improvement over traditional refinement methods.
Xerion CEO and co-founder John Busbee said: “Our technology is not just an incremental improvement – it is a fundamental reimagining of how we produce critical minerals.
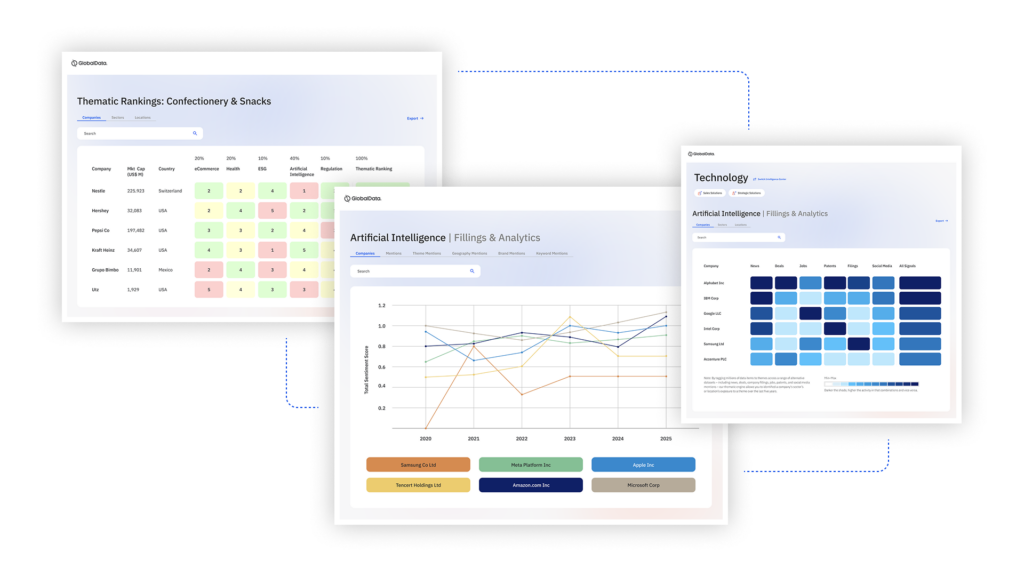
US Tariffs are shifting - will you react or anticipate?
Don’t let policy changes catch you off guard. Stay proactive with real-time data and expert analysis.
By GlobalData“At Xerion we are passionate about the advancement of a domestic battery materials supply chain, and we are proud to be addressing a critical national security challenge by presenting a solution that can significantly reduce our dependence on foreign mineral supplies.”
Xerion’s technology comes at a critical time as the US aims to reduce dependence on foreign mineral suppliers, according to the company.
The US currently lacks domestic cobalt refining capacity, while China holds 72% of global refining capacity. Furthermore, the US relies on complex supply chains for key minerals essential for defence and commercial applications.
The DirectPlate MSE technology also presents considerable environmental benefits. The low-temperature process significantly reduces electricity requirements and minimises permitting risks for commercial development.
Additionally, the closed-loop rinse system offers water use advantages and the absence of organic solvents contributes to a favourable emissions profile.