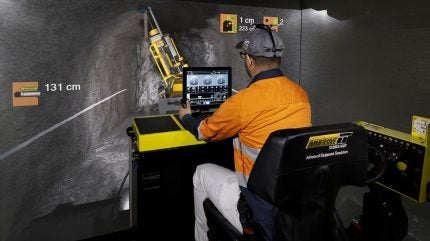
The mining simulation market has seen a boost over the past few years, due in part to increasingly stringent health and safety standards, as well as the rise of digitalisation and Industry 4.0 allowing engineers to put more intricate tools in the hands of operators.
Immersive Technologies is one such mining simulation company, leveraging the increasingly popular tools of virtual reality (VR), digital learning and 3D imaging to provide virtual training environments for underground miners. These training simulators allow miners to experience a range of potential events and accidents, preparing them for emergency situations from the safety of above-ground facilities.
The company launched its latest simulation platform, the IM360+, at this year’s MINExpo at Las Vegas (see event report). According to the company, its new platform is the first underground mining simulator to combine head-tracking technology with photo-realistic graphics to create a more life-like VR training environment than ever before. The platform also uses stereoscopic 3D imaging, which means a pair of 2D images are shown to the left and right eye to create a single 3D view – giving the illusion of depth.
We spoke to members of the team to find out more about the tech, and how emerging tech is changing safety standards in the mining industry.
Scarlett Evans (SE): Can you tell us about your IM360+ simulator?
Immersive Technologies (IT): We recognised that customers in underground, as well as mixed surface operation mining, need high-fidelity training solutions. The IM360+ is our answer to that.
By combining 360-degree surround display, photorealistic enhanced graphics with stereoscopic 3D imaging and head tracking technology, we were able to create an immersive training environment that closely simulates real-world conditions.
What sets the IM360+ apart from other technologies on the market is its high fidelity and versatility. It provides a level of sensory immersion and realism that we believe is unmatched in the underground training space – making it an ideal solution for operations involving mixed mining activities, or those transitioning between different types of mining.
The reason fidelity is important is because when graphics lack realism, it can impact depth perception. So, for tasks that require fine motor skills, realism is quite a significant element of increasing training retention.
Stereoscopic 3D, as well as head tracking, allows the user to see the training simulation from different angles as their head position moves – removing any realism barriers.
SE: What kind of challenges face underground miners that simulation aims to solve?
IT: Underground miners encounter a variety of challenges that can significantly impact safety and productivity. Limited visibility, confined spaces and the operation of complex machinery are just a few of the difficulties they face on a daily basis. These conditions require operators to have excellent depth perception and spatial awareness to avoid accidents and ensure efficient production.
By simulating the exact conditions miners will face, the IM360+ addresses these challenges, enhancing natural depth perception to create a highly realistic training environment.
The IM360+ also helps trainees develop the necessary skills to navigate confined spaces and operate machinery safely. This includes tasks such as drilling, bolting and production loading using load-haul-dump machines.
The ability to move position while looking around parts of the machines and assess angles accurately is required in underground operations. Creating realistic training reduces the likelihood of accidents and machine abuse, leading to improved productivity and machine availability.
In summary, we believe the simulator will be a transformative tool for the mining industry, addressing the unique challenges of underground mining.
SE: This year your company secured contracts in the US, Canada, Chile and Indonesia – can you tell us any more about these projects and how your tech will be used?
IT: We secured these underground training contracts in the second and third quarters of 2024. In these projects our simulation technology will be applied to address three main things – workforce attraction and screening, helping with new operator onboarding and compliance training, and optimising the workforce to meet production, safety and maintenance targets.
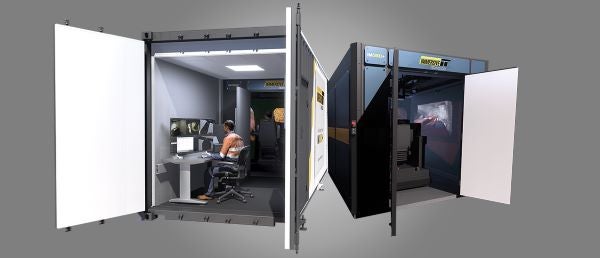
SE: How has the mining training landscape changed over the past few years?
IT: Demand for training has been on the rise for several reasons. Globally, many mining hubs are experiencing skills shortages, making training a persistent challenge in the industry.
The compounding effects of an ageing workforce, increasing role complexity due to new mining technologies, and the need to recruit and develop talent from other industries have strained the available talent pool in a number of global locations. Therefore, effective training and suitable upskilling strategies are key to ensuring a highly proficient workforce.
SE: How has the rise of digital tools impacted mining systems? How do you anticipate digital tools will further impact these systems in the future?
IT: The rise of digital technologies has transformed mining but has also introduced significant complexity, creating challenges like cognitive overload for operators.
We are looking to address these challenges with blended learning solutions that reduce cognitive strain while ensuring training remains engaging, relevant and effective – especially for a younger, tech-savvy workforce.
To achieve this, we are combining digital modules with advanced simulator training and in-field application to help miners transition from conceptual knowledge to practical proficiency.
These digital modules use chunked learning design to break training modules down into bite-sized pieces, which allows miners to master individual concepts before progressing to more complex systems. By using interactive virtual content and immersive experiences, this model mitigates cognitive strain and also caters to the learning preferences of younger miners.
Looking ahead, digital tools are expected to further impact the design of mining systems by enabling more sophisticated data analytics, predictive maintenance and automation. These advancements will require miners to redefine roles and retrain people to use this new technology.