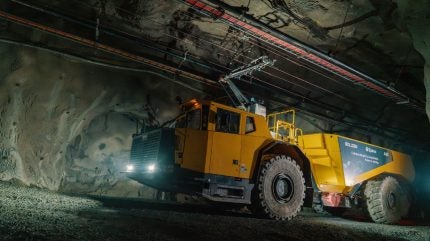
Mining finds itself in a unique position: essential to the energy transition, it also adds significantly to the burden of climate change. With requirements to cut its emissions by 90% of 2020 levels by the middle of the century, mining is awash with carbon reduction road maps and strategies. Yet paradoxically, it is required to do this at a time when demand for its produce is set to skyrocket. Copper and nickel demand, for example, is expected to rise by as much as 300% over the same period.
Today, mining is on a drive to increase efficiencies, use renewable power, promote circular economies – and electrify.
Back in 2020 there was a “growing” and “immediate demand” for low-emissions solutions, according to the Electric Mine Consortium (EMC), but technology and manufacturing capacity was hindering that, and in many instances “constraining the supply response”.
Part of research and analysis provider State of Play, the EMC was a collection of more than a dozen leading companies with a mission to accelerate progress towards fully electrified, zero-carbon dioxide (CO₂) and zero-particulate mines.
It says that although mining accounts for 8% of global carbon emissions – not to mention the risks emissions pose to mining crews underground – its 2020 State of Play: Mine Electrification report unequivocally showed that the industry can play its part through electrification, supplied by renewable energy.
However, in 2024, the EMC ceased, handing the baton to the mining industry and its equipment suppliers. As it did so, despite believing mining could rise to the task, it warned that renewables penetration in Australia was still less than 10%, adding that aside from pilot and prototypes there were no fully electric load and haul equipment fully integrated at mining operations.
“The next stage is serious and sustained capital investment in decarbonisation,” it said. “Across the Australian industry, there is a clear consensus that the major barriers to progress are the capital cost and the confidence in new electric equipment.”
What are the barriers to electrification of Australia’s underground mines?
Speaking with Mining Technology today, Graeme Stanway, former director of EMC and the founder of State of Play, says there are still unique challenges Australia faces: “[The] main one for underground [is] the deep declines, compared with shaft mines more common in North America.” But another – again using North America as the benchmark – is the lack of policy incentives, leading suppliers to prioritise other markets.
Globally there were 263 electric loaders (LHDs) and 68 electric trucks operating in underground mines as of July 2024, according to Mining Technology’s parent company, GlobalData.
In its Development of Electric Vehicles in Mining update it said the largest combined populations were in Canada (101), China (82), Russia (52) and Sweden (32). In a November 2023 analysis, Australia had just 16 operational electric mining vehicles, placing it fifth by some distance, despite being the fourth-largest miner behind China, the US and Russia.
Australia’s mining landscape, particularly the size and scale of haul trucks, presents unique challenges compared with other regions, according to ABB’s global eMine sales manager Ratna-Kanth Dittakavi.
“However, the technology is advancing rapidly,” he says. “Battery electric vehicles [BEVs] are becoming more powerful, and trolley systems are increasingly viable for underground operations, where they can provide the high energy demand required by large fleets.”
Other barriers to full-scale adoption also exist, including the large capital expenditure, according to Dittakavi, and the use of a reliable, sustainable green energy supply. “Mines need to source electricity from renewable sources to truly benefit from electrification, which can be challenging in remote areas.”
Battery technologies also need to improve in terms of energy density, cost, charging speeds and scalability to be viable for heavy-duty equipment.
Finally, Dittakavi says electrifying a mine’s fleet can impact operations such managing the expanded energy grid, integrating new technologies and training staff to handle equipment.
Marc Cameron, senior vice-president of resource industries sales, services and technology at Caterpillar agrees. “One of the biggest challenges when deploying battery electric technology is thinking through energy management, especially reducing the impact of charging events on site productivity,” he says.
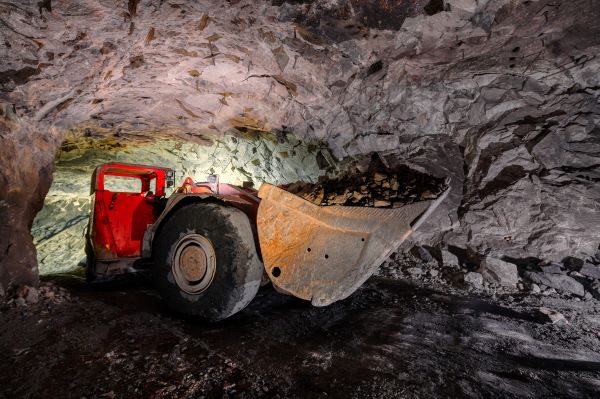
He says that, in an electrified landscape, all machines and processes are interconnected and interdependent, while electrical loads can include stationary processes, tethered machines and mobile battery-electric machines.
Another impact on operations, aside from the infrastructure, is less obvious initially, yet perhaps even more consequential. Cameron says while the innovation of zero-exhaust emissions equipment is exciting and critical to the overall solution, the problem to solve is much larger than a battery truck alone. “Each mine site is different and as customers deploy electrified solutions at site, the way they operate will have to change.”
Hoping to overcome these challenges, Caterpillar says it has been engaging customers earlier in the development process, under its Early Learner programme. “These collaborations are allowing our customers to have unique access and the ability to provide critical feedback,” says Cameron. He adds that the programme is currently at an exciting phase as “Early Learner trucks” begin to arrive at customer mine sites.
In late 2021, Caterpillar and Colorado-based Newmont entered a partnership that the miner said would “transform mining with a comprehensive mining system”. That alliance is on course to see the delivery of 26 first-of-a-kind battery-electric autonomous vehicles across Newmont’s underground and open-pit mining operations at the Tanami mine in Northern Territory, Australia, by 2027, according to GlobalData. The two have already announced the successful demonstration of a prototype at Caterpillar’s proving ground in Tasmania.
Industry and OEMs partner in the quest for mine electrification
ABB has also been working with Australian customers on various studies and proof of concepts to adapt technologies. “These tests are crucial in validating the potential for fully battery electric operations in Australia, where the technology could significantly reduce emissions and improve energy efficiency,” Dittakavi adds.
Such partnerships support Stanway’s notion that the technology is already there; it is more a case of getting the “adoption flywheel going” and then accelerating it. However, he says commercial partnerships are “very fruitful”.
Although there are still some hurdles to cross, a fully electric mine seems closer than ever. Offering no exhaust fumes, significant noise reductions and even reduced vibrations, the benefits are clear. Most importantly, the cut in greenhouse gas (GHG) emissions is significant if mining is to decarbonise. “Fossil fuel-driven fleets are the biggest contributors,” says Dittakavi. “Fleet electrification is the answer.”
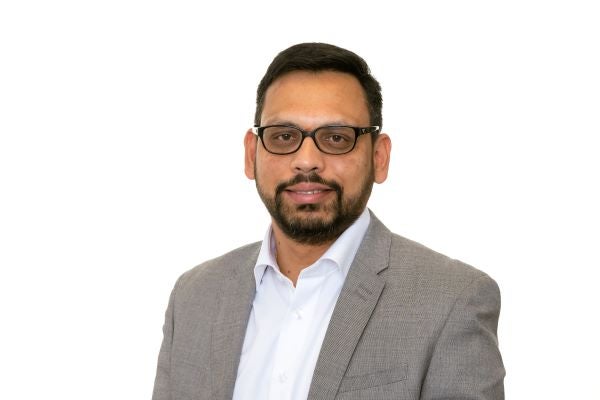
Asked whether electrification of mining in Australian has been slow, as some have suggested, he believes there is reason to be positive. “Australia has actually taken a front step in exploring and pushing for the innovative solutions,” he notes. It is collaboration that will see the country’s mines, with their unique challenges, achieve an electric revolution.
“So why was the EMC disbanded?” Mining Technology asked Stanway. “Compared with when we started, the members now had their road maps. The ecosystem of engineers and consultants, which did not exist at the start, had been set up; and operators had moved to more targeted and smaller collaboration with suppliers rather than a broad-based collaboration.” However, he again highlights that the remaining challenge is “getting the adoption flywheel going”.
For Dittakavi, collaboration both inside and out of mining will be critical. He says ABB strongly believes decarbonisation of mining cannot be solved alone. “These strong collaborations will bring innovative, reliable and sustainable solutions not only at an accelerated pace but also based on open standards to be interoperable and agnostic.” It is a statement Stanway, and likely Australia’s miners, would agree with.
However, Cameron shares one note of caution: “It is important to remember that everyone is on their own unique energy transition journey and will face unique challenges and opportunities.” He says Caterpillar continues to learn – it seems that is a position most in mining will likely remain in for some time yet.