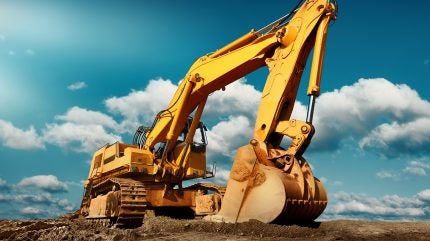
Ground engaging tools (GETs) are a critical element of mining tools. Used as attachments to industrial-scale machinery, they work in concert with diggers, excavators, scrapers, bulldozers and loaders almost on a constant basis to support the continuous and productive operation of a mine.
Examples of GETs include adapters, capable of breaking the ground at a range of depths; bucket teeth (tips), providing additional strength and, importantly, shock absorption for loaders and excavators; cutting edges, in a variety of shapes and sizes, for grading and scraping; grader blades, increasing operational efficiency in ground breaking and often used in conjunction with other tools; and rippers, providing added protection to machines as they shred materials.
They are all designed to protect expensive, critical machinery and help prevent lost productivity, improve performance and guard against unplanned maintenance and risks to worker safety.
A good maintenance regime is essential for GETs
The nature of the work GETs do, often round-the-clock, can be hard on them. Australia’s Cutting Edges, which has been supplying the earthmoving and mining industries for more than six decades, warns that although GETs are intended to protect equipment, if they are worn out or not fit-for-purpose they can lead to damaged assets and reduced output.
On its website, the company says well-maintained GETs can drive productivity and safety, cut down on unplanned maintenance, all while helping to preserve the lifetime of machinery by reducing stress on engines, linkages, hydraulic hoses and other assemblies.
However, it says, scheduled maintenance is still key; starting with the machine operator. They should, during their initial machine walkaround once on shift, visually check for “excessive or uneven wear or damage to buckets, tips, edges and adaptors; any loose or missing hardware or components; cracks on edges or welded joints; damaged or missing retainer bolts or pins; and missing adaptor covers”, Cutting Edges says.
It is a view shared by US-based parts and equipment supplier Prime Source, which says that good upkeep of GETs is vital to ensuring they remain in a safe working condition. In a blog, it says written maintenance logs can help track what has been done and when, and serve as a reminder for upcoming maintenance needs.
It seems that although – relatively speaking – they can often seem small in comparison with other parts of the heavy machinery, GETs play a significant role and so maintenance is key. For example, if even the smallest component or part of a component finds its way into the materials processing cycle, it can result in significant downtime and even injury.
Today, technology is increasingly aiding maintenance objectives across mines, including GETs. Digitalisation is providing actionable, real-time insights, and sensors, connected to each other and wider infrastructure management platforms, are continually feeding data for analysis and, when required, response.
Digitalising GETs to improve productivity and maintenance
GETs, although somewhat difficult to connect and thus not quite as advanced, are improving thanks to the march of digitalisation in mining equipment.
Australia-based CR Mining (now owned by Epiroc), for example, already offers X-Calibre, something it says comes free with all product purchases. It gives users real-time maintenance and performance data from any of their CR Mining products in a standardised form.
The reports, shared with customers via the X-Calibre app on mobile devices, help build a picture of a product’s operational health, highlighting potential issues before they become problematic.
Company representatives visit sites where its equipment is being used on a weekly basis, meaning they are also able to inspect and report on the conditioning of GETs. The reports, shared with customers via the X-Calibre app on mobile devices, help build a picture of a product’s operational health, highlighting potential issues before they become problematic.
Combining its GET Trakka, Orion Data Analytics, Titan 3330 and X-Calibre, the company hopes to provide live and automated reporting that will enable “smarter, faster”, and “more confident decisions” on maintenance, as CR told Coal Age in 2022. The insights don’t just cover maintenance, however; they also provide a wealth of data on operations and even individual operators.
This data, collated and stored remotely via the Orion data analytics platform, gives enhanced fleet and operations oversight, with actionable analysis. Performance metrics include truck payload compliance, ensuring vehicles are being loaded efficiently; productivity, right down to swing and load times; individual operator metrics, which may help better target training; and machine equipment fatigue, identifying issues and helping manage them until repairs are needed.
Bringing IoT and AI technologies to GETs
However, it is perhaps the GET Trakka system that is CR Mining’s biggest GET-specific innovation. The company says lost teeth and other GETs can result in lost productivity, unplanned bucket maintenance and even “catastrophic safety risks”. GET Trakka promises real-time bucket tooth and shroud monitoring for the “fast and safe location and recovery of broken GET”, preventing them reaching the crusher for wheel loaders, backhoes, face shovels and electric rope shovels.
Immediately alerting operators to the loss of a component through its network of Internet of Things (IoT)-enabled sensors, the part can then be located through what the company says is a world-first portable scanner. The system helps prevent these components causing damage further along in the cycle, whilst alerting operators to the loss of components, meaning further machine damage is less likely.
LoaderMetrics uses AI combined with thermal imaging to offer missing tooth detection across loader fleets.
CR Mining isn’t the only supplier employing cutting-edge technologies to digitalise GETs. Acquired by Weir in 2021, Motion Metrics’ most recent offering is the ShovelMetrics Gen 3. Like the GET Trakka, it monitors wear and alerts operators to risks from missing GETs by “allowing problematic material to be diverted away from the crusher”, according to the company.
“Additionally, the system continuously monitors tooth wear, affording mines the opportunity to avoid unscheduled maintenance, further reducing costly equipment downtime,” Motion Metric says. It largely does this though an “advanced high-definition bucket camera” that improves the system’s particle size analysis and boulder detection accuracy.
Other functionalities include payload monitoring; cutting the likelihood of equipment collisions with live surveillance views through its blind spot reduction capability; what the company says is the “world’s first ever lip shroud monitoring system”, cutting downtime due to crusher jams; and the ability to record and store up to three days of video footage.
The company’s catalogue of products also boasts LoaderMetrics, which uses AI combined with thermal imaging to offer missing tooth detection across loader fleets. “Our proprietary lens cleaning system ensures accurate performance under the harshest environmental conditions,” the company says. “We build our hardware to meet or exceed military standards for temperature, shock, vibration and dust.”
New market entrants take on GETs digitalisation
However, it isn’t just the globally renowned companies innovating in this space. Branding itself the first Australian IoT online store, S5 System has a product aimed at the mining and construction industry in its catalogue, too.
It is currently preparing to launch GETsmart, a robust non-invasive, real-time, wireless GET sensor system designed to protect from extreme temperatures, pressure, shock, water, dirt ingress and vibrations.
Placed on GET and overseen by an in-cab monitor that alerts operators to breakages and loss, the system can analyse the use of GETs while helping to prevent excessive downtime due to incidents or overlooked maintenance.
S5 System says the system has a minimal footprint, networking, power and installation requirements; can be fitted to almost any GET product and self-maintain; can operate in difficult environments; and offers a portable missing GET locator.
GETs and their use are changing thanks to the rapid spread of new technology. Well-established suppliers and new entrants alike are using these advances in ways that the sector could only have dreamed of just a few years ago.