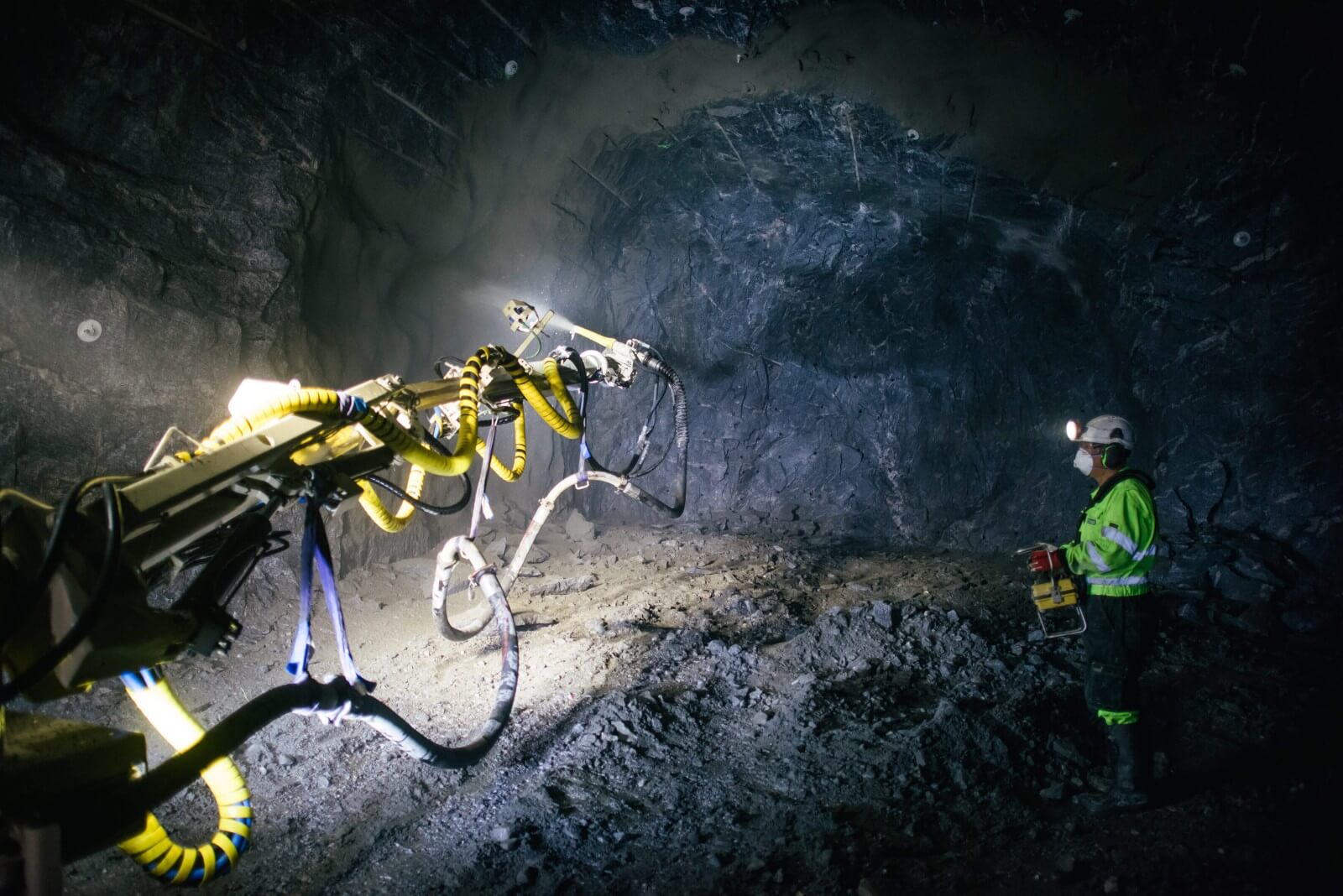
Efficient concrete spraying requires not only specialist equipment but also highly skilled operators. Spraying involves materials and conditions that vary over a wide range of factors, such as the quality of rock surface and corrugation, the required layer thickness of the concrete, aggregate mix quality and properties, as well as often difficult working conditions.
Accomplishing an even surface by spraying, requires constant and accurate monitoring of the thickness of sprayed concrete, while also maintaining the correct angle and distance. Not to mention other factors such as ensuring correct dosage settings, concrete pump speed and compressed air volume.
Promoting excellence in this area requires not only the correct preparation of materials, but also utilizing the most comprehensive training available and implementing the very latest in technology.
Sprayed concrete process expertise
Everything starts with the materials and getting the mix correct is vital for concrete spraying. “When we come to a new batching plan, we’ll always have a look at the aggregates and the sands that we’re going to be using,” says Ritchard Hood, director of spray concrete process for Normet International, a specialist in concrete mix design, who also supply technical advice and operator training.
Grading of the sand is checked using sieve analysis and plotted into a combined grading curve. “If we can get a line with the quality of the sands going straight up through the middle, then we know that our mix is going to be good,” says Hood. Attention to detail is essential: “To have a good, cohesive, stable mix, you need to eliminate any segregation or bleed, so the particles are supporting each other.”
Moisture content is also extremely important and must be accounted for in the mix.
After adding super plasticizer, the mix can be sent out for use, but once delivered, further checks are carried out, including temperature. “You should be looking for a temperature of 22 degrees”, explains Hood, “It helps with the hydration and helps the accelerator kick off the early strengths.” This is followed by measuring flow and flow spread.
By paying such attention to detail and ensuring that all these processes are completed successfully, the mix is now ready for on-site, with accelerant and lubrication added just before spraying after a final mix to ensure homogeneity. Spraying is remote controlled by a ‘nozzleman’ with final penetrometer tests taking place across sections of the sprayed area.
Operator training
An experienced nozzleman is highly skilled, and one way to improve processes and increase efficiency is through training. To this end, Normet has developed its own concrete spraying, virtual reality (VR) simulator, approved by both EFNARC (the international association of Experts for Specialized Construction and Concrete Systems) and the Swedish Rock Engineering association training program (certifying authority of sprayed concrete process in Sweden).
Using a VR headset, trainees can practise using the same set up as real-world equipment. As well as safety hazards to avoid, such as standing too close to the moving spray boom, the trainee can spray concrete layers, aiming for accurate layer thickness control. One unique property of a simulator is that trainees can try anything in a risk-free environment without wasting material or damaging equipment.
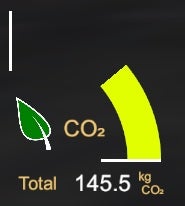
Trainees use the simulator to aim, keeping the concrete jet close to a 90-degree angle and at the right distance to the rock surface, one of the key elements to successful spraying, in order to achieve a good concrete build-up and compaction on the rock surface and avoid rebound, which is wasteful.
During training, waste and other environmental impacts can be established by using a Co2 calculator. This allows trainees to reduce their ‘green impact’ through more accurate and efficient spraying.
Training session results are later available as detailed reports to aid operator improvement, with an experienced and fully trained nozzleman greatly contributing to reducing waste and costs.
Concrete thickness control with Smartscan
Another important innovative at Normet has been the introduction of smart technology. Normet’s SmartScan and SmartSpray technology solutions provide automated calculations and monitoring of applied sprayed concrete thicknesses to improve efficiency and reduce wastage through over-spraying. SmartScan guides the operator to achieve the right thickness with the first application.
On-board, on-line diagnostics ensure that operators can always work at their optimal level by constantly checking that parameters are correct and even documents the quality of the concrete lining for project stakeholders.
Additionally, SmartScan allows operators to safely scan concrete thickness to check for any necessary corrections. SmartSpray Pro, has increased automation features, including auto-nozzle, while the latest model, SmartSpray ProPlus, has a fully automatic spraying function for defined areas.
By using expertise to prepare concrete, make training easier and safer, and transform efficiency through technological innovations, Normet is ensuring that spraying operations are safe, efficient, and sustainable.
For more information about equipment and services that Normet provides, download the whitepaper below.