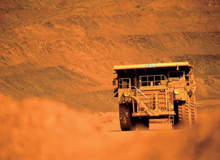
Over the last few years there has been a trend towards larger-scale mining operations as companies seek better economies of scale and, more recently, protection against the sort of price shocks that occurred as a result of the economic crisis.
Output from these larger operations is expected to reach peak levels over coming years as markets return to normal and the developing economies of China, India, Brazil and others continue to challenge supply. Considerable investment in new technology and infrastructure, however, will be required if miners expect to meet these challenges.
In the area of road transport, a new generation of clever monster truck is emerging to reflect increased on-site demands. Lighter vehicles with larger capacities, better fuel and tyre efficiency and sophisticated on-board computer systems for maintenance and automated operations are some recent improvements.
Truck automation is an important new area for the mining industry, with a number of first-generation vehicles in use at sites around the world.
The key to automation
In 2008, Caterpillar entered a partnership with Carnegie Mellon University’s Robotics Institute to develop automated versions of its large haul trucks, with the two organisations anticipating being able to automate vehicles with capacities up to 240t, and possibly beyond, in coming years.
Researchers at Carnegie will be adapting perception, planning and autonomous software architectures originally developed for the US military. Caterpillar says the research will build on an existing autonomous mining haulage system it is developing with BHP Billiton.
The mining giant expects to see deployment of automated trucks at some of its sites by next year. Rio Tinto has also been using driver-less trucks from Komatsu at its iron operations in the Pilbara, Australia, for over a year and reports positive results.
While there have been teething problems in other parts of the world, there is a growing feeling that automated trucks could be safer and more environmentally friendly, not to mention significantly more efficient and easier to maintain.
Standard on every Komatsu mining vehicle is the Vehicle Health Monitoring System (VHMS). Using a satellite communications system and optional wireless download, the Komatsu VHMS allows technicians to use a simple internet web interface to easily check pressures and trends, summarise the previous day’s payload and be instantly alerted of critical faults.
Caterpillar’s new Cat ADEM A4 has 50 times the computing power of its predecessor. The new module monitors more than 30 critical engine functions, drives the 20 fuel injectors and communicates more than 100 engine parameters that describe engine health and assist in diagnosing problems. With physical demands on mining vehicles expected to increase, it would appear this is the way forward.
Bigger is better
Mining trucks are expected to dramatically increase in size over the next few years, a fact that will have interesting implications for the future development of automated systems.
While Caterpillar and Carnegie Mellon are looking to automate trucks with capacities of about 240t, it is not inconceivable that much larger trucks could be controlled remotely in future.
Belgian mining equipment manufacturer Liebherr claims its flagship T282B is the world’s largest diesel electric truck currently in production, with a load capacity of 363 metric tons (equivalent to the weight of more than 210 minivans).
Standing nearly 8m tall, this truck is 15.3m-long, runs on a set of six 4m tyres and is powered by a gigantic 3,650-horsepower diesel engine. Liebherr mining equipment analysis and simulation manager Dr Vladimir Pokras says the scale is enormous. “It’s like driving a two-storey house,” Pokras says.
One of the primary requirements when designing these giant machines is that total vehicle weight cannot exceed tyre capacity. Every kilogram shaved from the vehicle structure can be added to the payload. The T282B is 12% lighter than comparable mining trucks. This is a distinct advantage, since lighter trucks save on fuel on their empty return runs and significantly extend tyre life. This is a major cost saver because such large tyres cost tens of thousands of dollars each.
Liebherr designs the vehicles so tyre wear is minimised by the kinematics of the dual parallel control-arm arrangement and by a differential driving wheel control system that automatically adjusts the torque and speed of traction motors when turning. Many manufacturers have also come to market with major improvements to engines, which typically boast better fuel efficiency and lower emissions.
As miners seek opportunities in more challenging environments, vehicles will be expected to perform more challenging functions. Mineral sands, for instance, are a rich new vein of commodities, but need new equipment and technologies in order to be properly exploited.
Consider trucks that traverse layers of clay and waterlogged peat to mine oil sands in northern Canada. Driving across the surface is often described as being like driving across a mattress. The engineering challenge lies in integrating advanced features such as the differential wheel control system into a lightweight truck that is still tough enough to handle the conditions. Most mechanical trucks would not be an option.
Electric versus mechanical
There is a growing feeling that diesel-electric trucks are often easier to operate and generally outperform mechanical trucks, especially on steep grades. They are also less expensive and usually easier to maintain, and offer better fuel efficiency and a smaller carbon footprint.
Liebherr reports that sales of its ultra-class diesel electric trucks have grown from to 10% to 15% in each of the last five years. Komatsu’s recently launched 960E-1 (960E) AC electric drive haul truck is the largest in its fleet, carrying a 360t payload and weighing 1,270,000lb when fully loaded.
“The 960E balances payload, productivity and power, and is designed to be the right match for today’s mining needs,” the company says.
A pioneer in the manufacture of mechanical mining trucks, Caterpillar recently made a number of important announcements outlining its roadmap for diesel-electric trucks based on the new 795F AC platform, which the company says incorporates a number of new technologies. Included are four-corner blended braking and retarding using Cat oil immersed and cooled disc brakes, as well as electrical retarding, improving safety and operator confidence.
In addition, the remote-mounted generator enables servicing without reckoning with other major components, while wheel motors mounted inside the axle allow final drives to be serviced easily and separately.
Caterpillar says it remains committed to mechanical trucks but stresses that its growing range of diesel-electric vehicles means it can satisfy a wider range of customer needs.
“Mechanical drive mining trucks will satisfy the needs of the vast majority of mining operations,” it says.
“But as the only manufacturer of 181-t and larger mining trucks with both mechanical drive and electric drive systems, we will soon be able to offer trucks that address all mining company preferences.”