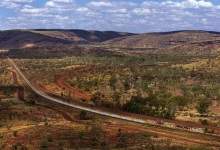
Rio Tinto” height=”287″ src=”https://www.mining-technology.com/wp-content/uploads/image-digitalinsightresearch/Archive/nri/mining/rio%20tinto.jpg” width=”431″ />
Maximising efficiency is tough in times of plenty. With so much money rolling in, focus is naturally drawn away from what is rolling out. Few industries support this better than the mining sector. Thanks to almost a decade of unprecedented high prices on global commodity markets, operators the world over have enjoyed record profits and prolonged periods of growth, without ever feeling the need to concentrate too heavily on what was going out.
Now that the cloud cover offered by those prices has receded, with market prices falling across the board, the implications of that oversight have been laid bare. In a recent study on the Australian mining industry conducted by global accountancy firm EY, formerly Ernst & Young, and the University of Queensland, it was revealed that productivity had dropped by roughly 50% over the past decade.
Capital productivity, the value extracted from equipment, machinery and facilities, has also fallen sharply, with the study reporting a decline of 45% since 2000. The same piece of research cited figures from a US study that showed that between 2009 and 2012, labour productivity dropped by 27.5%. In short, productivity has not been high on the boardroom agenda over the past ten years.
That is set to change. As the memory of those high prices fades ever further away, productivity piques interest. From upping labour output to cutting waste, maximising productivity is the order of the day. And there are already a number of companies, technologies and innovations that are showing the way.
Using big data to down disruptions
In collaboration with mining equipment operator Thiess, IBM has developed a package that combines real-time analytics with a network of sensors connected to mining excavators and trucks. In contrast to periodical approach to monitoring equipment, where scheduled assessments are carried out, IBM analyses data in real time and makes detailed predictions about the integrity of specific pieces of equipment by measuring load weights and abnormal usage.
How well do you really know your competitors?
Access the most comprehensive Company Profiles on the market, powered by GlobalData. Save hours of research. Gain competitive edge.
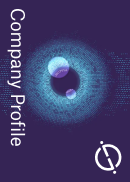
Thank you!
Your download email will arrive shortly
Not ready to buy yet? Download a free sample
We are confident about the unique quality of our Company Profiles. However, we want you to make the most beneficial decision for your business, so we offer a free sample that you can download by submitting the below form
By GlobalDataEmerging market companies are drastically outperforming their counterparts from the developed world .
With the cost of an unexpected breakdown of an excavator coming in at around $5m a day, the potential savings from just that area are significant. With similar sensors and analytics solutions being developed across the operations process, the opportunity to cut downtime and increase production is huge.
Generating power onsite
As with all energy intensive industries, powering operations weighs heavy on profitability. In order to increase its energy efficiency, while at the same time reducing its carbon footprint, Chilean mining firm Antofagasta Minerals has turned to renewable power generation. Having already tapped into wind power, the company recently penned a deal with SunEdison to build a 69.5MW solar plant at its Los Pelambres copper mine in order to help it meet its goal of drawing 30% of its power from renewable sources.
The company also plans on adding hydro power to its arsenal. To further maximise energy savings, companies are also adopting lighting control systems, using more efficient air conditioning, utilising variable speed drives to reduce usage and collecting more accurate data on energy use in order to identify inefficiencies.
Maximising material lifetimes
Following a recent trial with Chilean copper mining company Codelco, DuPont has shown that Kevlar conveyor belts can increase capacity by 18% while cutting annual maintenance costs by 60%. In addition to the productivity benefits, the use of Kevlar belts also reduces the amount of energy consumed.
PatricioPorta, specialist-operations analyst within the management of plants division at CodelcoAndina, said: "In mining, conveyor belts must go down into the bowels of the earth. Copper ore is sharp and hard on equipment used to extract it. The belts we have installed are durable and strong, they make a great impact on our production."
Simulation of operations brings success
To boost both productivity and safety within its roughly 1,600 strong workforce at its Red Lake gold mine in Ontario, Canada Goldcorp has been capitalising on the benefits of simulated operations. Employing ThoroughTec Simulation’s CYBERMINE containerised system, the Canadian miner has trained up new staff away from the dangers of real-life conditions, while also ensuring that old hands keep to standard. The approach has enabled the company to reduce safety risks while also trialling new and more efficient operational procedures in a safe and less costly environment.
Joel Campbell, training operator at Goldcorp, said: "For two days we put them through their paces and evaluate them on different scenarios. This gives the operators a chance to familiarise themselves with the controls and learn correct operating techniques. We need to ensure that they’re ready to operate the scoop safely and productively."
Making the most of your minerals
Having already led the way in automating operations with the development of driverless trucks and trains, Rio Tinto’s Mine of the Future programme is now focusing its attention on extracting greater value from its mines. As part of the strategy, the mining giant recently launched bespoke 3-D mapping technology to maximise the amount of iron ore it extracts from its operations. The package will enable it to precisely identify the size, location and quality of ore in real time. The solution will link a network of sensors spanning from the drills underground to the trucks transporting it. Rio Tinto hopes the technology will enable it to focus its efforts and resources on higher grade ore and ensure high levels of productivity.
John McGagh, head of innovation at Rio Tinto, said: "This technology allows us to quickly and easily view, compare and evaluate data to paint a picture of what’s under the ground – it’s like an ultrasound image of the deposit delivered in real-time, something that we could never do before."
A new technology developed by Australia’s national science agency will make the process of treating mining wastewater cheaper, faster and greener.
Long-term goals or short-term gain?
From machinery to minerals to the miners themselves, the industry has a wide range of options to boost productivity. Technology has made a number of previously impossible tasks possible and cut a number of corners that would previously dampen efficiency, and new ways of working offer the chance to develop a safer and more productive workforce.
But it is on the industry to take advantage of what is open to it. With budgets tighter than before, the tension between planning for the long term and playing short is tightening, but those that make more from less are likely to profit.