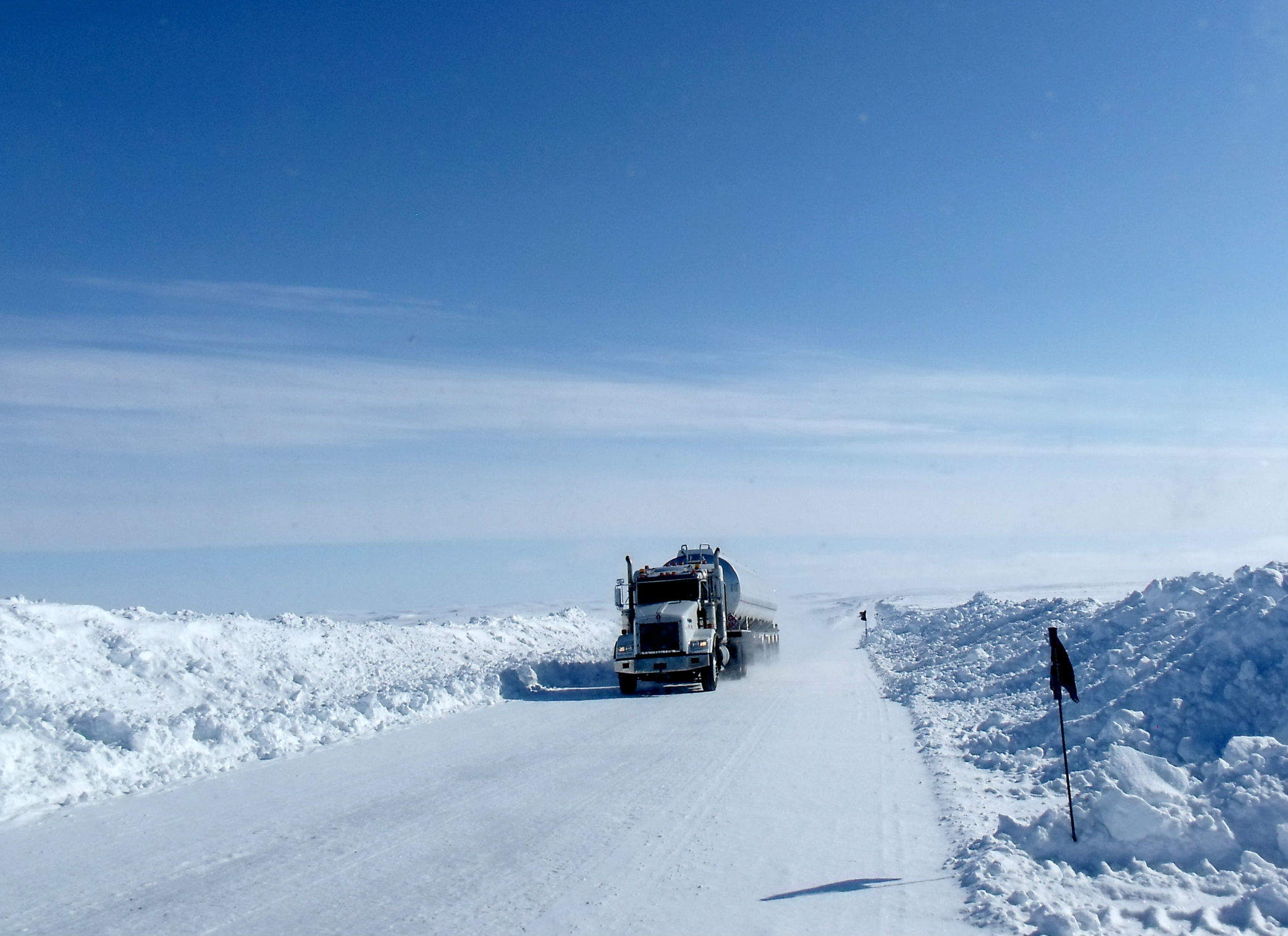
No resource is infinite, and as a result, miners are having to dig deeper and make discoveries in increasingly challenging conditions. All of the easily accessible deposits have been extracted, so mines are now often set up in places where the environment can be extreme and difficult for workers to endure.
In some mining locations, temperatures can dip below -50°C, where there are treacherous surroundings and a real chance of frostbite. In other places, ambient rock temperatures can reach up to 55°C due to encompassing magma. While up high on mountain plateaus, miners and machinery alike struggle to obtain sufficient oxygen to get the job done.
It’s a necessity to stay efficient and effective in the face of these challenges, and mining companies and their contractors are always coming up with ways to ensure workers are safe and that mines remain profitable even in the most dangerous locations.
The big freeze: Arctic mining
The rewards to be reaped in the far North can be massive. One company that’s very familiar with working in Arctic conditions is Nuna Logistics, which provides construction and mining support services to the mining industry in Canada.
Nuna’s vice-president of business development Grant Pearson says the challenge of working in the cold climate does not come from the weather itself, but from the logistical issues that arise as a result of the remote locations.
"In many cases there is no access via all-weather road, therefore supplies can only be mobilised on a seasonal basis via ice road in the winter months," he says. "Remote Northern mines also have all-year-round aircraft access but cost and size restrictions do not always permit shipping via air freight."
Freezing temperatures can cause hydraulic lines to burst and overcooled engines can lead to early component failure. Even a minor repair job can be disastrous if supplies can’t be accessed easily. So, all replacements need to be stored on-site, otherwise parts would need to be delivered by cargo planes, at high expense.
For example, at one mine situated above the Arctic Circle in Hope Bay, Nunavut, the only way of getting equipment to the site is by a sea lift at a port which is only clear from ice for six weeks of the year.
"Good planning is mandatory to ensure re-supply goods and materials are shipped when required," Pearson says. "There is only one opportunity to do so unless the product can be flown in."
At another northern location, Nuna was managing the mobilisation of supplies via sea lift, which Pearson says was an "incredibly complicated logistical challenge".
"The largest vessel to ever pass through the Panama Canal was part of this sea lift," he says. "Sea lifts in the Arctic are limited in many cases to an approximate three-month ice-free period which further complicates the logistics of shipping."
He adds that "These challenges were overcome through complete integration with our client and excellent planning from all parties involved."
Pearson says that special Arctic-grade winter fuel and equipment is prepared for these conditions, and are necessary to ensure continuous operation in extreme winter conditions. Some technologies can help operations, such as ground-penetrating radar, a method that uses radar pulses to detect the reflected signals from subsurface structures and build up an image. It is used to profile ice thickness and road alignments during construction.
Safety and warmth for workers
Worker protection is paramount in freezing conditions, so each task has to be reviewed extensively before activities start. Pearson says this procedure is actually true of all operations, regardless of the temperature. In the Arctic environment though, everyone is specially equipped with suitable Arctic clothing, and outside exposure is kept to a minimum.
"In fact, prior to even getting on the plane to fly to a remote Arctic location, one must have the appropriate clothing and footwear to be allowed to board the aircraft," says Pearson. "Most employees are in heated equipment, however if it is necessary to work outside, exposed skin is minimised and crews are trained to watch each other for signs of frostbite."
‘Warm-up shacks’ are also in operation to ensure employees can be kept safe and warm, and everyone works with a partner and frequently checks in with their supervisors.
Regardless of the challenges, Pearson says that in many ways, extreme freezing temperatures can be an asset from an engineering perspective as they can provide access to otherwise inaccessible locations. Building ice roads and constructing dams using frozen centres as a core are practical ways of taking advantage of the cold climate.
Can’t take the heat
On the other end of the scale, many mines now have to dig deeper to reach profitable deposits of minerals. Ultra-deep underground conditions are humid, damp and dirty, and the deeper the mine the higher the ambient temperature.
Rock temperature in deep mines can get very high, especially when they are situated near volcanic rock. For example, Glencore’s Kidd Creek Mine in Canada is 3,000m deep and surrounded by magma where ambient rock temperatures reach 55°C.
Engines do not work well in extreme heat. Refrigeration systems are usually in place to cool the air to 30°Cor less, but due to the humidity it is still necessary to minimise the time that both people and equipment have to work before stopping to cool down.
The intense heat puts a strain on ventilation systems; energy expenditures account for about 40% of a Canadian underground mine’s operating costs and 80% of that is spent on airing the place out.
It may be acceptable for machines and equipment to work in unforgiving heat, as parts can always be replaced and fixed. It is a different story for workers though, who must take regular breaks to stave off exhaustion.
At Australia’s deepest mine in the Mount Isa mining complex, shafts can reach 1,800m underground. The amount of infrastructure and high-tech equipment required to keep mining operations going in such conditions is staggering; the 5m by 5m tunnels are large enough to drive through and there’s over 1,000km in the network.
Mines in Sudbury, Canada can get even hotter because there is some evidence of magma sitting below the Sudbury basin. This molten rock keeps anything built on top of it very warm.
Enter the robots
One way to combat increasingly dangerous mining environments is the adoption of more automation within the mining sector. Back in 2012, Centre for Excellence in Mining Innovation CEO Damien Duff told the Canadian Institute of Mining: "Tests have been done for years to demonstrate remote operation of some of the equipment. The technology exists, but can we do it reliably or effectively all the time? That’s the issue."
Since then, technology has come a long way and many companies such as Rio Tinto and BHP Billiton are bringing in more robotic technology such as driverless trucks and automatic drills.
With this, mining companies are killing two birds with one stone; ensuring workers aren’t being put in danger, and labour costs are reduced, which has positive implications for mine operations that are struggling to turn a profit in the midst of a commodity downturn.
While jobs may initially be lost, automation could actually open up new, safer positions for workers who can adapt to an ever-evolving industry.
The reality is that different areas of the world, including under the sea or in mountainous regions, are going to have to be exploited to keep up with the global demand for minerals. If this means moving into extreme environments, then companies are going a long way to ensure it is effective and safe, but the future of mining may look very different in a few years if robots are able to take on the dangerous jobs.