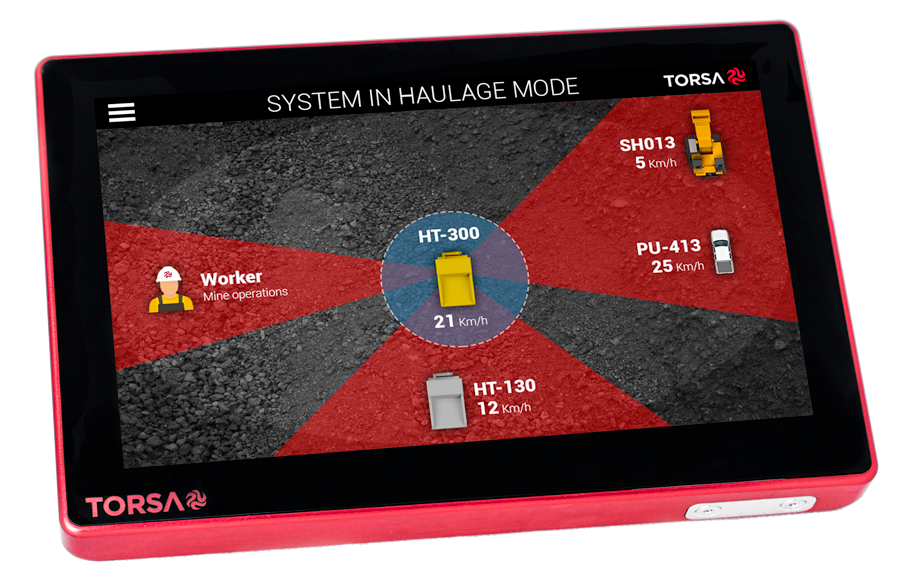
Mining companies have certainly been reaping the rewards in terms of more sophisticated machines and increased productivity, but they also serve as reminders of underlying safety as incidents of vehicle collisions remain higher than they should be.
In the past, the technology was limited but now a collision avoidance system (CAS) is able to alert an operator or machine when there’s a potential issue, providing a far sharper awareness of their surroundings.
And with 200-tonne trucks morphing into 400 tonnes, as well as shovels growing in size, this goes some way to addressing the logical concern that with larger vehicles come more blind spots.
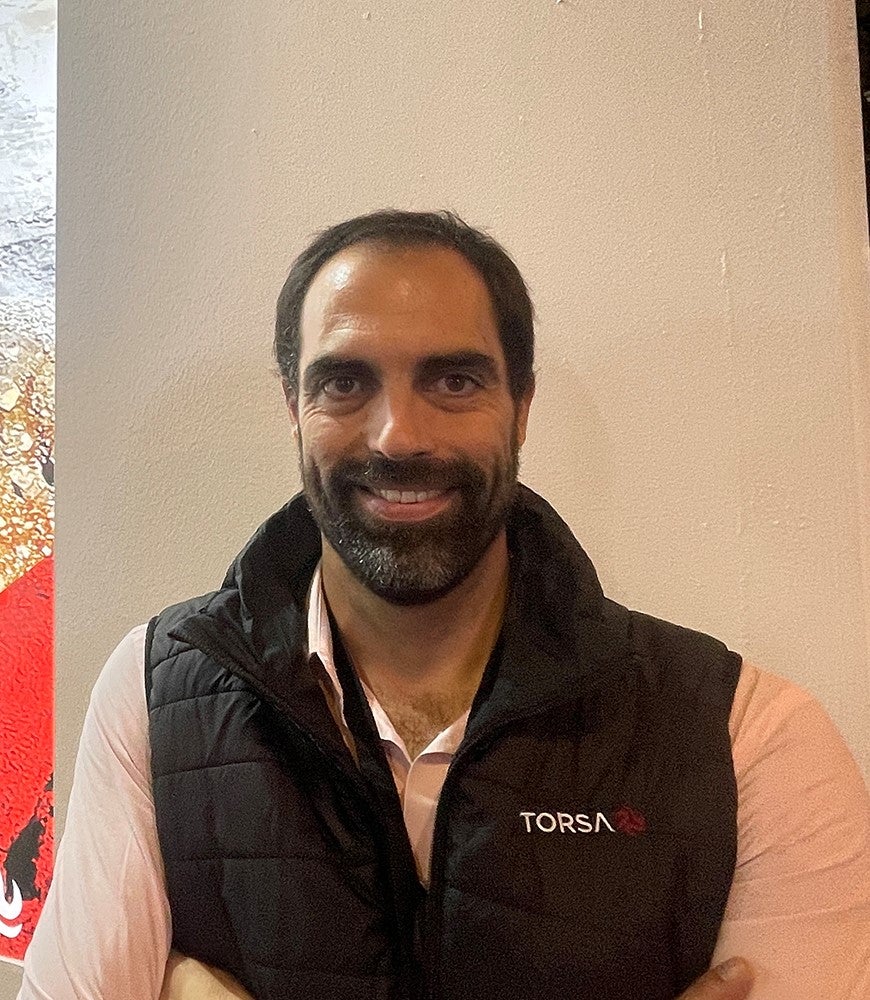
“At this point in time, it’s a question of alerting the operator when they have a problem. But in the future – or now, if the customer requests it – we could stop a shovel from turning by taking remote control if, according to our system, there’s likely to be a crash,” says Gabino de Diego, director of business development at Spanish engineering company TORSA.
This high-precision solution is especially useful in reducing the risk of shovel interactions with bulldozers, trucks, mining fronts or even large rocks. Based on, among others, high precision GPS-RTK and light detection and ranging (LiDAR) 3D technology, the solution provides the shovels with eyes, generating a profile of the surroundings, says de Diego. All the sensors are installed to cover a full, 360-degree view, that sits directly in front of the operator. This is simulated beforehand using a digital twin of the vehicle to ensure all angles are overseen before the real-time digging begins.
TORSA’s system is fully flexible and can be customized depending on the requirements of the customer: for bulldozers in particular “we implement two-way communication between the operators of a bulldozer and a shovel so they can talk to each other during the cleaning process,” he explains. And as an additional protocol, one party alerts the other before starting; this is a further safety boost to the sensors.
TORSA’s CAS is designed to perform at Intervention Control Level 9 (according to a programme of safety requirements listed below). Shovel-bulldozer interaction is an instance where CAS could take control and halt the movement of the shovel when the bulldozer is nearby.
On the right wavelength
LiDAR technology works by collating precise, consistent readings to produce in-depth data, while remaining immune to environmental variations. TORSA began using the mark one version – 2D LiDAR – in 2015. With that, says de Diego, “it was like you were sending a disk of light and anything cutting through that disk would be detected as an object”.
In 2019, the upgraded 3D LiDAR was installed, in which data ‘points’ are fed back and processed at a rate of “900.000 a second, so it’s much more accurate than a disk,” says de Diego. LiDAR was invented for military use, he explains, where “you would have needed a very wide field of view, so when you take that to an environment such as a mine, you basically detect everything”.
TORSA’s strict adherence to a Vehicle- to-Vehicle (V2V) protocol ensures the ability of the embarked systems to talk between each other. Indeed, returning to the advantages of two-way communication between vehicles using CAS, de Diego points out that each operator knows its own data, including speed, position etc, but, crucially, also the data of other operators. He says that their calculations rely on the safest distance between trucks and the safest stopping/braking distance – both well-known equations that have been adhered to for over 40 years. “It’s not like we’ve come up with something revolutionary; we use something that’s very well documented,” he says.
It is unique in its ability to calculate not only the appropriate time to stop when faced with a risk but also that the machine is running at a safe distance compared with the vehicle or mine front. “So based on our conditions, we calculate our stopping distance, then based on information from other vehicles, we can ensure the distance between ourselves and the vehicles or the front is safe,” explains de Diego.
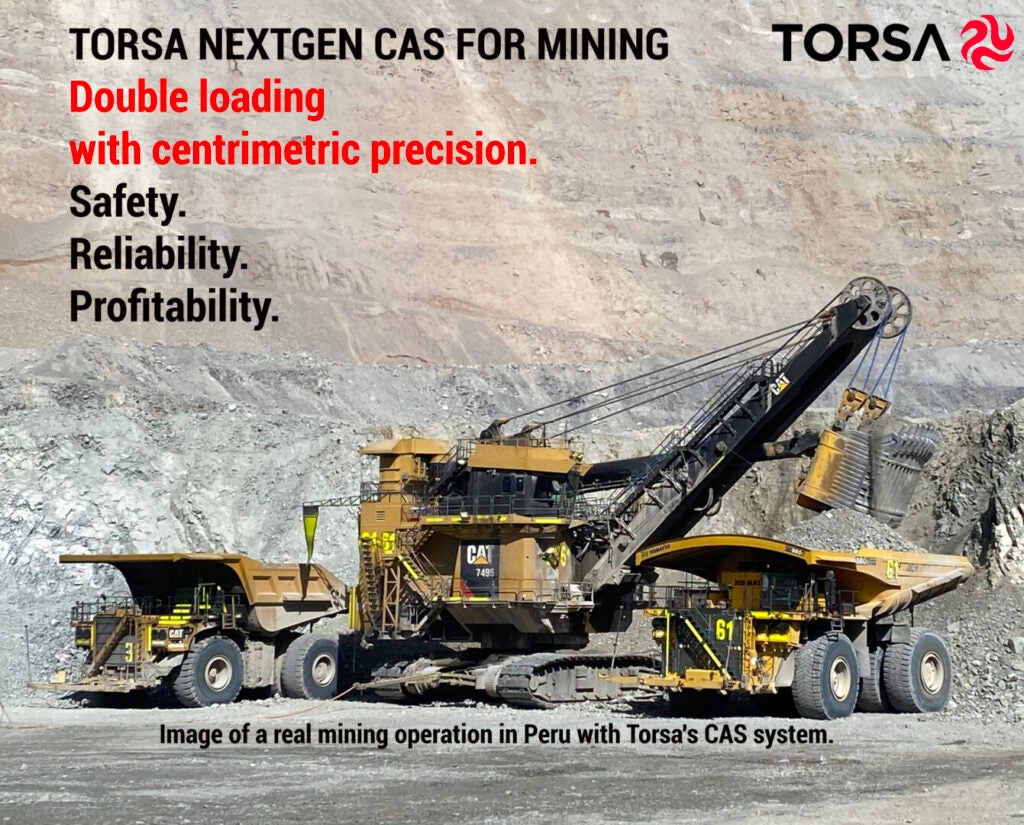
Being able to access the data of other vehicles means that the system can compute contextual information, such as a queue while waiting to be loaded, where the usual rules may not apply, rather than sending out needless alerts, which makes for a much better user experience. TORSA´s system has been designed taking into account feedback obtained during a number of hours working with machinery operators.
A standard three-tier alert process reports and communicates developments to machines as they arise: sending a message of awareness, prompting the user to stay focused on the road; providing a low-level alert to adjust speed or position in order to avert a collision; or issuing a more urgent, warning message to modify behaviour immediately to avoid a crash.
Security for different scenarios
Depending on the function – be it, say, loading, positive slope or haulage – companies may demand a customised design of their CAS. In such cases, TORSA achieves the best outcome by collaborating closely with that particular client, explains de Diego. A protocol is defined: the client might inform TORSA about its loading process, emphasising that in order to protect its machinery, the track can be no closer than 5 metres.
“We then adapt our system according to the mine’s requirements, so it will be shown as green on the display at that safe distance of 5 metres or more. We adapt according to the mine, we don’t make anything up,” de Diego says.
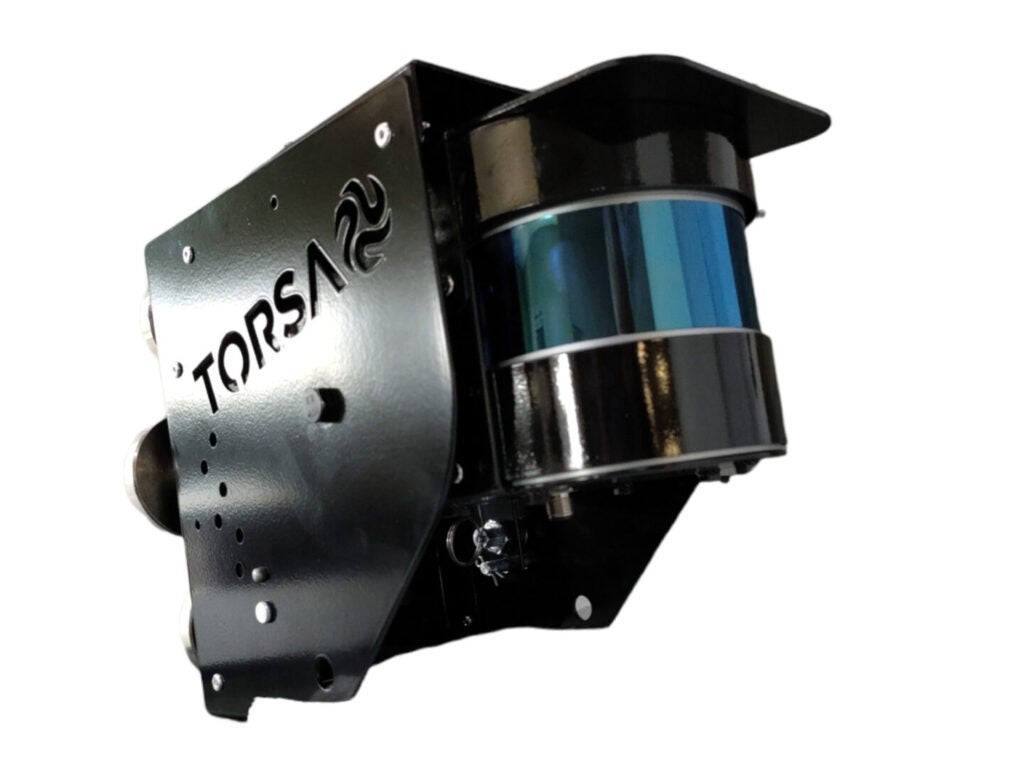
In an underground mine, the number of sensors is scaled up as it isn’t possible for location technology such as GPS to work below ground level. The network includes cameras, ultra-wideband radio positioning technology and LiDAR. “That combination makes up for all that information we have from GPS. The galleries are really tight, whereas in an open pit they’re obviously not so tight, so you have to be very accurate underground.”
TORSA’s system is the only tag-less system in the market. For non-tagged machines that cannot ‘talk’ to others, LiDAR provides accurate readings for individual operators. “Underground, we have what we call trigger sensors, which give you an idea that there’s something around you. Then we have measuring sensors, which are alerted by the other sensors and will start measuring the distance you are from the object or person. For tagged machines, there will be vehicle-to-vehicle interaction, too, where they are able to talk to each other using Radio Frequency (RF), which can help locate the vehicle in the absence of GPS,” says de Diego.
TORSA implements the ISO 21815 standard (which covers detection of objects, warnings to the operator, intervention control and test procedures). CAS simply sends a message to a data interface which is usually provided by the original equipment manufacturer (OEM).
In these machines the nuanced braking decision is made by the OEM’s interface.
TORSA’s commitment to safety requirements
TORSA works with the International Council on Mining and Metals (ICMM), where it participates in the Innovation for Cleaner, Safer Vehicles (ICSV) programme. This includes more than 27 global mining companies and technology suppliers aiming to accelerate the development of a new generation of mining vehicles.
The safety requirements based on the ICSV following the Earth Moving Equipment Safety Round Table (EMESRT) comprise nine levels of incident preventative controls.
These are:
- site requirements;
- segregation of controls;
- operating procedures;
- authority to operate;
- fitness to operate;
- operating compliance;
- operator awareness;
- advisory controls;
- and intervention controls.
The TORSA CAS solution is designed to work at levels 7 to 9.
Future thoughts
For now, cameras, CAS and fleet management systems are installed with their own separate displays, meaning the number of screens in a vehicle’s cabin is approaching overload.
De Diego believes that the industry’s OEMs will already be working hard to integrate all of these aspects into one all-encompassing unit. He uses the automotive sector as an example: “If you have a car, the infotainment system is not designed by the manufacturer, it’s produced by maybe Bosch, LG or Samsung. We envisage the same for collision avoidance”.
In the medium term, de Diego predicts there will be a pool of suppliers such as TORSA collaborating with OEMs in order to integrate various networks into one interface to fit new equipment, thereby resulting in one expansive system. There will be a market for retrofitting these all-in-one interfaces on to older vehicles, he adds.
Looking through a long-term lens, CAS will become even more crucial for autonomous mines running remotely, believes de Diego. Today the operator is able to take control, but in the near future, where remotely operated mines might be thousands of miles from the hub, it will be necessary to factor in a time lag.
“If you are relying on a 5G network with 10 milliseconds lag and, for some reason, that increases to one second. Now, how are you going to operate machinery with one second lag? You need a CAS to stop the vehicle and take control of it,” he explains.
Further details:
For more information, please visit torsaglobal.com.