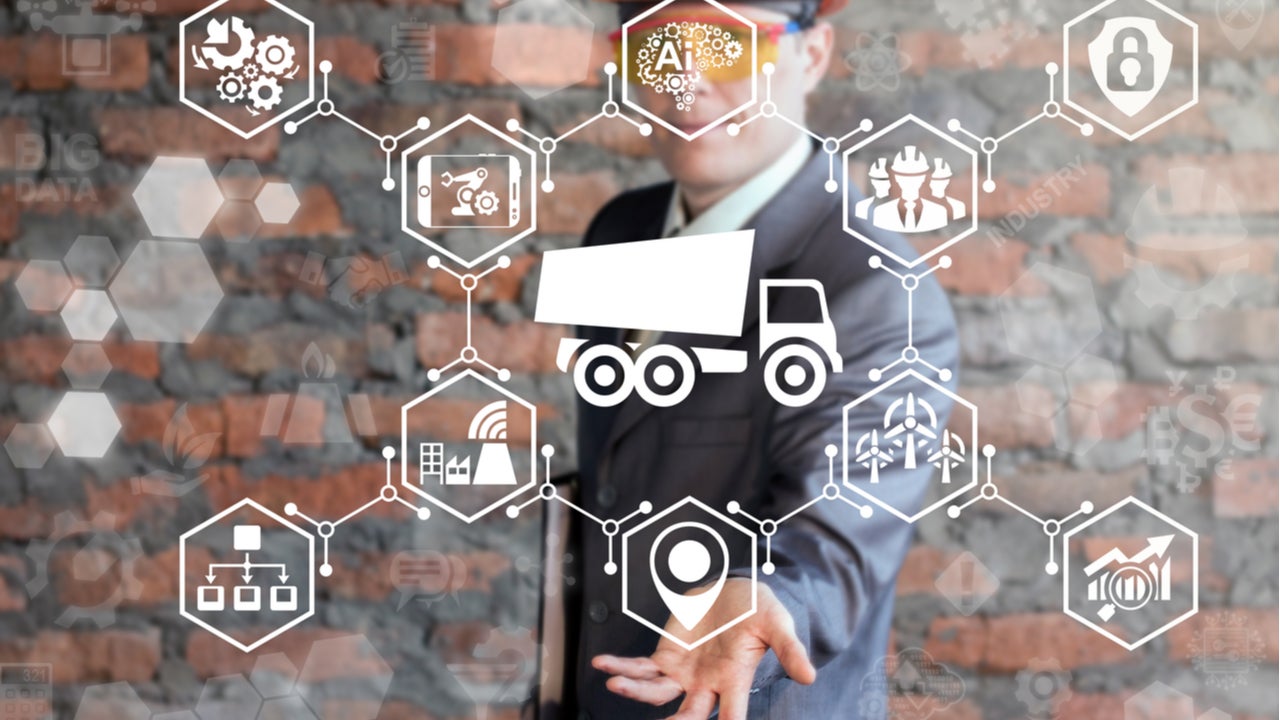
Artificial intelligence (AI) and digitalisation has transformed the way that mines operate. Safety, productivity and sustainability are all key factors that mines continually strive to improve, with optimisation through leveraging data being at the forefront of driving innovation.
Digital transformation relies on collecting data and using relevant information to optimise processes and improve new equipment development. Not only does digitalisation change the way that we collect data (by enabling us to collect much more and in real-time with Internet of Things (IoT) technology) but AI, machine learning, and advanced analytics tools means that we can make use of vast amounts of data.
For mining technology company Normet, leading global transformation with digitalised and sustainable mining is its core ethos. Mining-technology.com spoke with Pekka Jaarinen, Normet’s director of digital services, and marketing manager Jukka Pihlava, about how Normet is striving to improve the efficiency of underground mining.
“We need to get the foundations right in order to push forward with innovations and improved processes,” Jaarinen explains. “On a global scale, we need to be collecting data and utilising this data to create more efficient processes.
“Digital transformation is a big spectrum when we’re talking about value-based processes, efficiency gains, safety issues and their lifetime costs. This all affects field operations and training needs, because if we utilise data and leverage data insights into more efficient processes and better performance, we can use this information to train our field or service technicians on operations better.
According to Pihlava: “We are already using digitisation and data for optimising processes, such as sprayed concrete underground. With that, we can improve safety and productivity, and long-term optimisation takes care of equipment and reduces lifetime costs.
“Digital transformation such as automation has also added a new way of working, and a new set of skills that our workforce needs to be trained in.”
Automation proves particularly useful when it comes to cumbersome, operations heavy processes. Normet’s SmartScan for sprayed concrete, which can monitor or in the future even automate the thickness of shotcrete, is a prime example of how automated processes can improve efficiency and reduce waste.
Advancements in simulation technology provides the industry with much safer methods of training, which not only protects trainees and expensive machinery, but enables efficient monitoring of trainee progress and feedback. EFNARC’s Nozzleman scheme, for example, provides the industry with effective simulation-based training for sprayed concrete that utilises advanced virtual reality (VR).
Normet is known in the mining industry for its innovative technology and equipment, and electric vehicles and machinery is one area that is growing globally.
“Electric vehicles are equipped with our latest digital features and innovation, and of course electrification is important, especially when talking about sustainability and environmental impact. Using that digitalisation, data and AI, we can make the operations and machinery even more sustainable in the long run,” explains Jaarinen. “We’re focussed on improving the research and development process around equipment so we can develop even better equipment in the future.”
“We have to think also about the safety of operators,” Pihlava adds. “More remotely controlled operations mean that we have less people in harm’s way.”
Normet continues to improve on its range of process services, from sprayed concrete to rock reinforcement and water control. For more information about sprayed concrete and the services Normet provides, download the whitepaper below or visit their website.