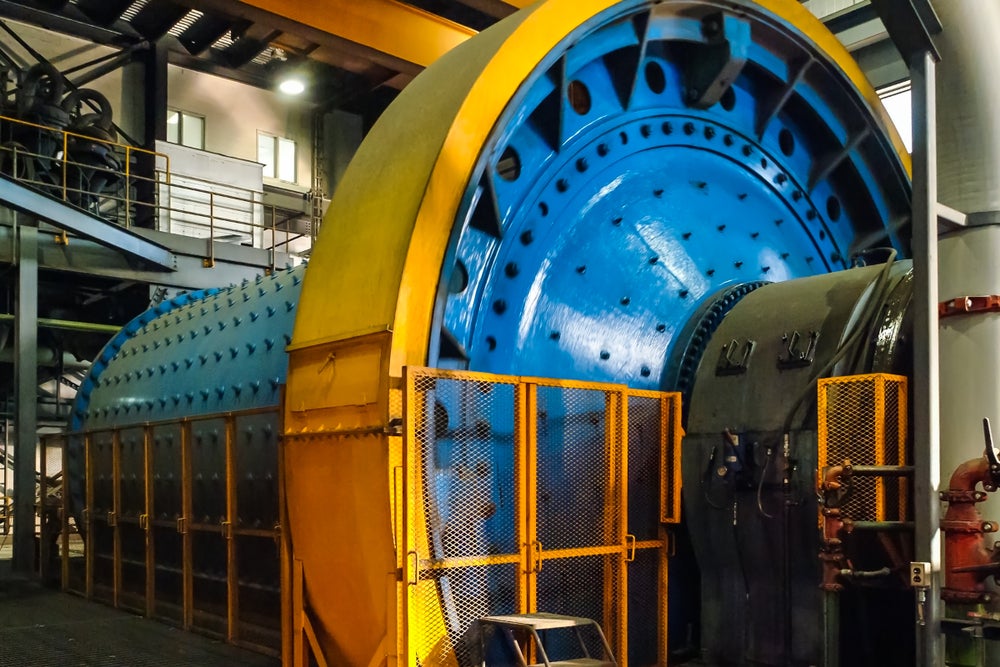
In an industry like mining, wear and tear on equipment is a given. With an optimal design, however, engineers can significantly reduce the rate at which their gear requires replacement, saving precious time lost in production outages.
And in a business where time is money, a solutions-oriented engineering company that’s able to identify the root of the problem and propose a superior design could make all the difference. When a uranium ore processing plant was having issues with its rock box chute liners, this is exactly how Castech Solution’s material engineering experts tackled the problem.
Rock boxes have an important role. As the material comes off the first conveyor, it falls into the rock box, whose primary function is to direct the flow to the centre of the next belt for further processing. Large volumes of abrasive materials, pumped with fluid to increase flow, slide through the rock box. To protect the chute from this abrasive material, plants use replaceable liners fastened to the inside of the chute.
The uranium plant’s Bisalloy 400 feed chute liners were wearing out at a frustratingly fast rate, something the operators had put down to the material’s high abrasiveness. But over a phone call with Castech, a different reason was discovered: the plant was recycling their process water, and it had a pH as low as 3.5. By asking the right questions, Castech realised that the liners weren’t wearing away; they were rusting due to the highly corrosive process water.
From there, Castech was tasked with redesigning the liners, starting out with a new material selection that was resistant to both erosive and corrosive wear. High-chrome white iron was specified due to its ideal properties in this regard, but as Castech’s general manager Allen Vaughan tells Mining Technology, that was only half the story.
“We then came up with a way of making the liners so that the highest-wear area was thicker, and the area with the least amount of material flowing through it was thinner,” says Vaughan. “This meant that the whole liner wore out at the same time. At the end of its campaign, it wears down to a consistent thickness all over so you’re not throwing away good metal that you’ve paid for.”
Another key aspect of the redesign was the staggering of the mating joints. “In the original design, all the liners were on the same line, which creates a long weak point when the material runs down that continuous line. When you create a discontinuous pattern of lines, like brickwork, you further reduce the amount of wear,” explains Vaughan.
A successful project
With each of these optimisations, the chute liner went from a previous wear life of five weeks to one lasting 16 weeks or more. “The customer was amazed,” remembers Vaughan. “Funnily enough, the liners were lasting so long that they were falling out because the bolts were corroding first! Because the bolts became the weak point, we then came up with a Hastelloy bolt solution that could survive the corrosive environment like the liners.”
The team’s close work with the customer, particularly in that early stage before the client themselves had even recognised the problem, was critical to the project’s success. Castech’s ability to quickly gain a solid understanding of the customer’s process limitations means an optimised design proposal is never far away.
“That’s one of the things I think Castech’s really good at,” adds Vaughan. “We’ve got a lot of experience, so we can sit with people and really get down to what we can do to help them. We draw on that experience and are able to implement solutions that may not be so obvious to people.”