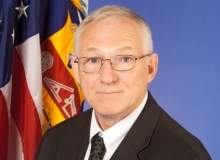
We’ve heard from several global mining conglomerates about how they are implementing important strategies into their sites to ensure their staff are protected from harm. Over the years they have acquired modern technologies and equipment to prepare workers for potentially dangerous situations and introduced multigas monitors, hazard detections systems and intelligent mine management software to decrease the risk of a life threatening event.
But, what are governments doing to improve health and safety in the mining industry?
US mining spokesman Joseph A. Main explains how his government is guiding workforces to prevent future mining disasters and provides details on the policies being enforced in the country to make sure miners are held accountable for violating critical safety standards
Sarah Blackman: What has the US learned from recent mining disasters?
Joseph A. Main: The history of mine emergencies has taught us that we can never be too prepared to respond to these life-threatening events. Despite the development of modern rescue equipment and techniques, gaps still remain that can hamper or harm a successful mine rescue effort.
The Pike River mine disaster consisted of a series of four mine explosions. There has been much speculation about the cause of these explosions ranging from pumps, cables, collapse, lack of methane drainage and so on.
We will not know for sure until the mine investigation concludes and a final report is published. However, we know communications and power were knocked out. Mine operators must design mines to prevent these types of events, conduct risk assessments to identify hazards and make critical systems more resilient and redundant.
How well do you really know your competitors?
Access the most comprehensive Company Profiles on the market, powered by GlobalData. Save hours of research. Gain competitive edge.
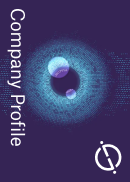
Thank you!
Your download email will arrive shortly
Not ready to buy yet? Download a free sample
We are confident about the unique quality of our Company Profiles. However, we want you to make the most beneficial decision for your business, so we offer a free sample that you can download by submitting the below form
By GlobalDataThe Copiapó mining accident in Chile involved the collapse of the one and only mine entry. The mine was located in a very remote area. Drillers and drilling resources had to come from great distances, some from the United States. A mine rescue capsule had to be fabricated in country to implement the escape.
Lesson learned – mining companies must maintain at least two escapeways at all times (a requirement in the US). Drilling technology needs to be identified before an incident occurs and arrangements with drillers should be made in advance. Pre-surveying, matching important locations underground with markers on the surface, is essential.
SB: In what ways would you say mining safety has improved over the last five years?
JM: During the last five years, mine safety has improved through, among other things, the implementation of the MINER Act, the use of impact inspections to target problem mines, a revamped pattern of violations programme and the Rules to Live By initiative.
In fact, according to preliminary data, 37 miners died in work-related accidents at the nation’s mines in 2011, the year with the second-lowest number of mining deaths since statistics were first recorded.
MSHA places a major emphasis on miner training and we have awarded more than $3m in Brookwood-Sago Mine Safety Grants since 2007. These grants are specifically aimed at providing the funding for education and training programmes to better identify, avoid and prevent unsafe working conditions in and around mines.
SB: How has safety equipment and technology improved during this period?
Since 2006, mine operators have been required to have post-accident two-way communications systems and tracking systems in all underground coal mines.
New technology in this area is evolving and improving rapidly. In addition, mine operators have replaced point-type heat sensors with carbon monoxide sensors in all underground coal mines and improved belt entry maintenance requirements, improved lifelines are now required for emergency escape, along with multigas monitors on all active working sections, and tethers, used for escape, operators have increased training for their atmospheric monitoring systems, and since January 2009, MSHA’s Approval and Certification Center processed 170 applications for approval of conveyor belts from 30 different manufacturers to meet new flammability requirements.
SB: What mining safety policies you are enforcing in the US?
JM: Most mine operators try to obey the law and operate a safe workplace. However, some operators take their obligation to comply with our regulations more seriously than others.
For those that don’t, we have developed progressive levels of special enforcement to bring mines back into compliance. If an operator does not improve compliance in response to regular inspections, or if there are other signals of compliance issues, they are subject to impact inspections, in which MSHA at times, sends teams of inspectors to ‘blitz’ the mine.
If a mine operator persists in non-compliance and develops a record of serious violations, the mine could be subject to MSHA’s potential Pattern of Violations (POV) process.
SB: What are the most important strategies that mine operators should apply to their sites in order to respond to an emergency situation?
JM: Mine operators must have a comprehensive mine emergency response plan (ERP), which is required by the Mine Improvement and New Emergency Response Act of 2006 and implemented by MSHA regulations.
The plan specifies how each mine operator will respond to a mine emergency, the communications and tracking system used at the mine, how post-accident breathable air is provided requires tactile, directional lifelines in the primary and secondary escapeways, training in mine emergency procedures, which mine rescue teams will respond to an emergency and where their mine rescue stations are located. Miners must be trained to escape first and take shelter as a last resort.
Mine operators must notify MSHA of a mine emergency within 15 minutes. The mine may need to be evacuated if a fire, explosion or inundation occurs.
Mine rescue teams are contacted and, once on the scene, put into action. The mine operator should take regular gas readings at mine fans, boreholes and other significant locations. Either the mine operator or MSHA may analyze gas samples to develop a trend analysis to determine what is happening in the mine, as accurately as possible.
A command centre is established, composed of the operator, MSHA, the state and, often, miner representatives. All mine rescue / recovery plans must be approved by MSHA and, in some cases, the state.
SB: How can mining companies reduce their rate of violations?
Under newly developed procedures, mines identified as having a potential POV are given ambitious goals to reduce the rate of serious violations.
We provide them guidance on developing a Corrective Action Program and give incentives for operators to implement effective programmes. If the operator meets its target, it can avoid being placed in POV status under Section 104(e) of the Federal Mine Safety and Health Act of 1977.
Missing the goal is serious, because once a mine is in POV status, MSHA issues a closure order for any area of the mine affected by an S&S violation until the mine completes an entire inspection without an S&S violation.
In addition, MSHA’s multiphase programme, ‘Rules to Live By’, focuses on 47 frequently cited standards that cause or contribute to mining fatalities.
The goal of RTLB is to reduce the numbers of deaths and injuries from the targeted standards by having mine operators identify and correct all hazardous conditions, direct MSHA enforcement towards confirming that violations related to these conditions are not present at mines and ensure miners are better trained to recognise and avoid these particular hazards.
SB: What are your hopes for mine safety this year, in terms of emergency response management and technology development?
JM: The mission of MSHA is to prevent death, disease and injury from mining and to promote safe and healthful workplaces for the nation’s miners.
Our aim is to assure that miners remain protected and return home to their families and friends at the end of every work shift. Ultimately, the goal is zero mine fatalities.
MSHA, the mining industry, state agencies and mine rescue teams must assess the resources, equipment, training and preparedness of all to identify gaps in mine emergency response preparedness and work collectively to bolster mine emergency response capacity.
MSHA has conducted several stakeholder meetings with industry, state agencies and mine rescue teams to identify the gaps in mine emergency preparedness and response.
This May, MSHA will implement a Mine Rescue Summit at the National Mine Health and Safety Academy in Beckley, West Virginia, to further explore where remaining gaps exist and develop plans to address any deficiencies. Key persons from industry, mine rescue teams, labor groups and state agencies will participate.